A natural marvel, cotton begins its journey in the fields as fluffy bolls on the cotton plant. Its transformation into the soft, versatile fabric we know involves a series of intricate processes.
From the crucial step of ginning, where seeds are separated from fibers, to carding, which aligns and cleans the strands, the evolution of cotton is a testament to human craftsmanship.
Spinning, weaving, or knitting follow suit, giving birth to the yarns and fabrics that shape our world. Cotton fabric gains color, patterns, and texture through dyeing, printing, and finishing.
This journey, from field to fabric, is a testament to human ingenuity and the enduring legacy of cotton in the textile industry.
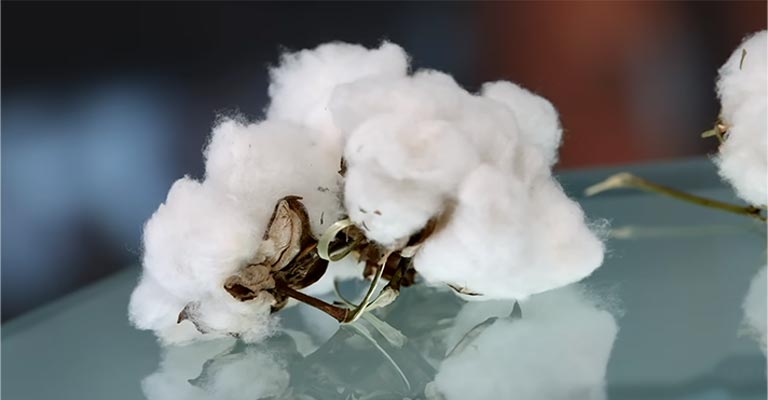
What is cotton?
Cotton is a natural, soft, and fluffy fiber harvested from the bolls of the cotton plant (Gossypium). It is one of the world’s most widely used and versatile natural fibers, valued for its comfort, breathability, and absorbent properties.
The cotton plant is cultivated in warm climates, primarily in regions like the United States, India, China, and Brazil. The fiber consists mainly of cellulose, a complex carbohydrate, and is composed of thousands of tiny, intertwined fibers.
These fibers are extracted, processed, and spun into yarn or thread, which is then woven or knitted to create a wide range of textiles, from clothing and linens to industrial materials.
Cotton’s significance in the textile industry and the global economy is immense, making it a vital crop for various industries worldwide.
How Is Cotton Turned Into Fabric?
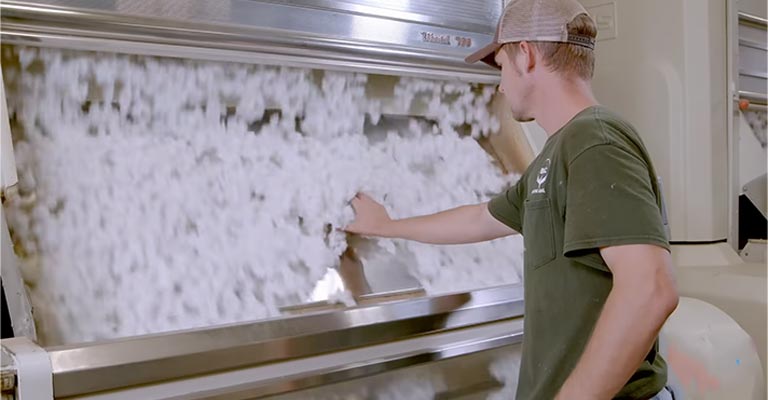
Cotton, one of the world’s most widely used natural fibers, undergoes a complex and fascinating transformation to become the fabric we wear every day. This process involves several steps, from cultivation in the fields to the final product on store shelves.
Let’s delve into how cotton is turned into fabric:
Cultivation and Harvesting
Cotton cultivation is a meticulous process that involves planting cotton seeds in well-prepared fields. The plants require adequate sunlight, water, and warm temperatures to grow optimally.
They are carefully tended to, with farmers monitoring for pests and diseases. Once the cotton bolls mature, skilled laborers hand-pick them to ensure minimal damage to the fibers.
Ginning
Ginning has come a long way from its early manual methods. Modern ginning facilities use high-speed machines that combine saws, air flows, and brushes.
These machines efficiently separate the cotton lint from the seeds, producing a raw material that’s ready for further processing.
Cleaning and Carding
The cleaned cotton fibers are then subjected to a rigorous cleaning process. This involves passing the cotton through various machinery equipped with rotating drums, brushes, and air jets to remove any remaining impurities.
After cleaning, the cotton fibers are carded, which entails passing them through a series of rollers covered in fine wires. This process not only straightens the fibers but also further removes any tangled or short fibers, resulting in a smoother sliver.
Drawing and Roving
Drawing and roving are pivotal steps in refining the cotton fibers. Drawing machines precisely control the speed and tension at which the slivers are pulled, aligning the fibers and improving their overall quality.
Subsequently, the drawn slivers are transformed into rovings. This process involves further stretching and twisting, resulting in a more uniform strand.
Spinning
The spun cotton yarn is created through a mesmerizing dance of machinery. Spinning frames twist the rovings into a continuous yarn.
The twist level applied determines the resulting yarn’s thickness, ranging from delicate, fine threads to robust, heavy ones. The yarn can be single-ply or plied together for added strength or texture.
Weaving or Knitting
The spun cotton yarn is now ready to be transformed into fabric. Weaving machines interlace the vertical (warp) and horizontal (weft) yarns, creating a tightly bonded textile.
The loom’s intricate movements determine the fabric’s pattern and structure. Alternatively, knitting machines work their magic by looping yarn together to create a distinct elasticity and drape fabric.
Dyeing and Printing
Fabric coloring and design are vital steps that add personality and flair to the material. Dyeing baths immerse the fabric in carefully prepared solutions, ensuring even and vibrant coloration.
On the other hand, printing processes involve applying patterns using screens, blocks, or other methods. The artistry of dyeing and printing transforms plain fabric into a visual feast of colors and designs.
Finishing
After dyeing and printing, the fabric may go through various finishing processes. Calendaring machines use heated rollers to smooth the fabric’s surface, imparting a polished finish.
Mercerizing, a chemical treatment with caustic soda, enhances the fabric’s strength, luster, and dye absorption capabilities.
Additional finishing chemicals may be applied to imbue the fabric with specific properties like softness or wrinkle resistance.
Quality Control
Quality control is integrated into every stage of production. Technicians and inspectors scrutinize the fabric for color consistency, texture, strength, and adherence to specifications.
Any deviations from the desired standards are addressed promptly to ensure the highest quality final product.
Cutting and Sewing
In garment factories, specialized machines are used to cut fabric panels according to patterns.
Skilled seamstresses then skillfully sew these pieces together, creating various clothing items, from shirts and dresses to trousers and jackets.
Packaging
Once the products pass the quality control checks, they are prepared for packaging. Packaging serves as a means of protection during transportation and a way to showcase the product to consumers. Labels, tags, and branding elements are added to enhance the product’s appeal.
Distribution
After packaging, the finished products are ready for distribution. This stage involves logistics planning to efficiently transport the items to retailers, wholesalers, or customers.
Distribution channels can vary widely, from local shops to global supply chains, depending on the scale of production and market reach.
Retail Display
Upon reaching retailers, the products are displayed for consumers to browse and purchase. Effective retail displays and marketing strategies attract customers and promote sales.
From clothing boutiques to department stores, the presentation of textile products is key to their success in the market.
Consumer Use and Enjoyment
Finally, fabric-based products reach the hands of consumers. Whether it’s a cozy sweater, a stylish dress, a set of bedsheets, or an industrial filter, consumers use these items daily.
The fabric’s comfort, durability, and aesthetic appeal play a significant role in determining customer satisfaction.
Botanical Origin of Cotton
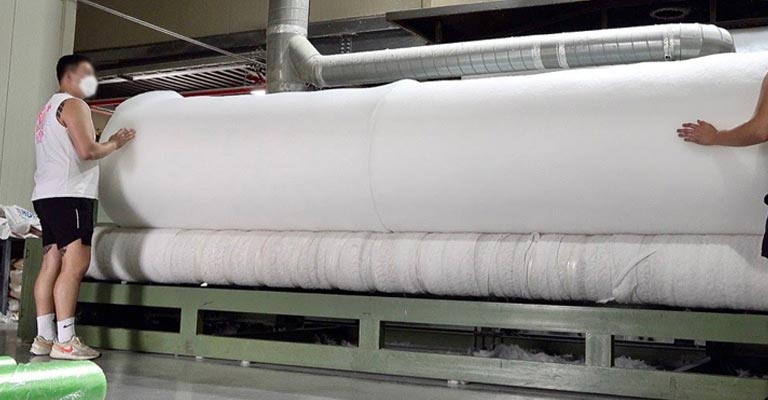
Cotton is a natural fiber derived from the bolls of plants belonging to the genus Gossypium. This genus comprises around 50 species, many of which are native to subtropical and tropical regions worldwide.
There are four main species of cotton that are commonly cultivated for their fibers:
Gossypium hirsutum (Upland cotton)
This cotton species is known for its adaptability to various growing conditions, making it the most widely cultivated worldwide.
Upland cotton plants typically have shorter fibers than other species, but advancements in breeding and cultivation techniques have led to improved varieties with higher fiber quality.
Gossypium barbadense (Pima or Egyptian cotton)
Pima cotton is highly prized in the textile industry for its exceptionally long and strong fibers. It produces a luxurious and lustrous fabric known for its softness and durability.
Native to South America, it has been cultivated in various parts of the world with similar climates, including the southwestern United States, Egypt, and Peru.
Gossypium arboreum (Tree cotton)
This cotton species is distinctive for its shrub-like growth habit, which can resemble a small tree. It is well-suited to arid and drought-prone regions, making it an important cotton variety in areas with limited water resources.
While it is not as widely cultivated as other species, its seeds are valuable for their oil content, which is used in cooking and industrial applications.
Gossypium herbaceum (Levant cotton)
This cotton species has a long history of cultivation, dating back thousands of years. It is well-adapted to drier conditions and is often grown in regions with limited water availability.
The fibers from Gossypium herbaceum tend to be shorter, but they have been historically used for various textile applications.
Historical Significance of Cotton
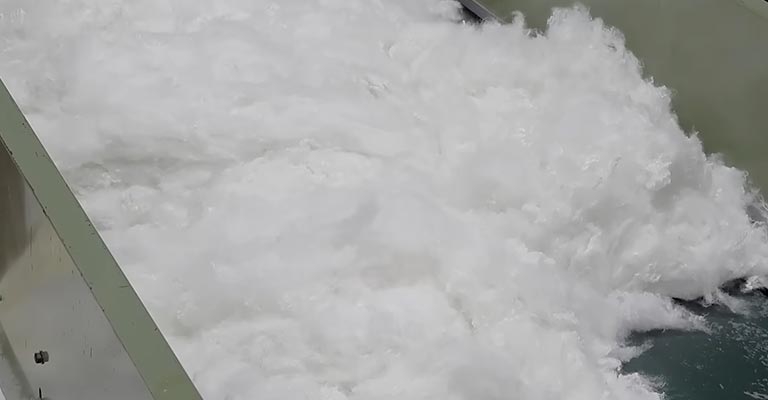
The history and legacy of cotton fiber are deeply intertwined with human civilization, spanning thousands of years.
Here’s an overview of the historical significance of cotton:
Ancient Origins
Cotton cultivation and use date back to ancient times, with evidence of cotton fabrics found in archaeological sites dating as far back as 6,000 years ago in the Indian subcontinent and the Americas.
Trade and Wealth
Cotton played a pivotal role in the economies of ancient civilizations, including the Indus Valley, Egypt, and the pre-Columbian cultures of the Americas. It was highly valued for its softness, comfort, and versatility in textile production.
Industrial Revolution
The mechanization of cotton production during the Industrial Revolution in the late 18th century led to a significant shift in global textiles.
The cotton gin, invented by Eli Whitney in 1793, revolutionized cotton processing, making it a more economically viable crop and fueling the growth of textile factories.
Slavery and Plantation Agriculture
The demand for cotton, especially in the southern United States, drove the expansion of cotton plantations and the use of enslaved labor.
This period of history is marked by the significant social and political consequences of the cotton industry, including the American Civil War.
Cotton and the Modern Global Economy
Today, cotton remains a crucial element of the global economy. It is a cornerstone of the textile industry, providing raw materials for clothing, household textiles, and industrial applications.
Challenges of Cotton During Turned Into Fabric
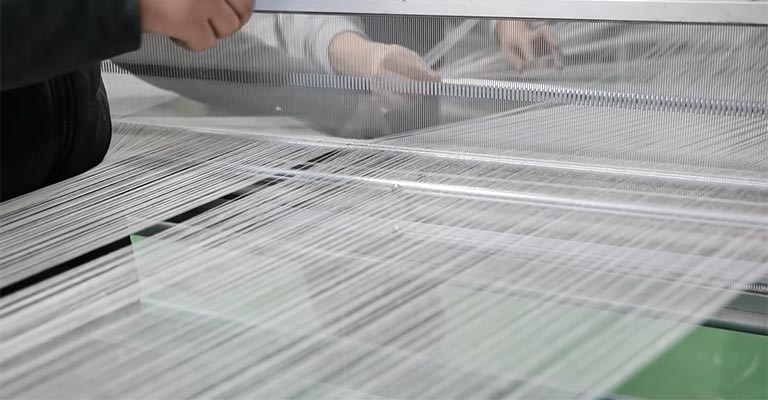
The process of turning cotton into fabric involves several challenges, spanning from cultivation to manufacturing. These challenges have implications for the environment, labor, and sustainability.
Here are some of the key challenges faced during the transformation of cotton into fabric:
Environmental Impact
Cotton cultivation often relies on intensive water and pesticide usage. The environmental challenge lies in reducing the ecological footprint of cotton farming.
Sustainable practices like organic farming, reduced water usage, and the use of non-GMO cotton varieties are emerging solutions.
Pesticide Use
Cotton is susceptible to various pests and diseases, leading to substantial pesticide application. This poses health risks to farmers and can harm ecosystems. Integrated pest management and developing pest-resistant cotton varieties aim to mitigate this challenge.
Water Usage
Cotton is a water-intensive crop, and its cultivation can lead to water scarcity in regions with limited resources. Sustainable water management practices, such as drip irrigation and rainwater harvesting, are essential to address this challenge.
Labor Issues
In some regions, cotton farming and harvesting rely on manual labor, often involving low wages and poor working conditions. Fair labor practices and ethical sourcing are vital to improving the livelihoods of cotton farmers and laborers.
Land Degradation
Continuous cotton cultivation can lead to soil degradation and reduced agricultural productivity. Crop rotation and soil conservation techniques are employed to mitigate this issue.
Chemical Dyeing and Finishing
The dyeing and finishing processes in textile manufacturing can be environmentally damaging due to chemical usage and water pollution.
Innovations in eco-friendly dyeing methods and adopting sustainable finishing techniques are addressing this challenge.
Energy Consumption
Textile mills consume significant amounts of energy in the spinning, weaving, and finishing processes.
Sustainable practices such as energy-efficient machinery and renewable energy sources aim to reduce the carbon footprint of cotton fabric production.
Waste Generation
Textile manufacturing generates substantial waste, including scraps and discarded fabrics.
The challenge lies in reducing waste through recycling and upcycling and addressing the disposal of textile waste.
Chemical Management
The use of chemicals in cotton processing can have adverse environmental and health effects.
Responsible chemical management and the development of eco-friendly alternatives are essential to minimize these impacts.
Supply Chain Transparency
Ensuring transparency throughout the cotton supply chain, from farm to finished product, can be challenging. Technologies like blockchain and traceability systems are being employed to improve transparency and accountability.
Future Trends and Innovations in Cotton Fabric
The textile industry, including cotton fabric production, continually evolves to meet changing consumer demands and sustainability concerns.
Several future trends and innovations are likely to shape the cotton fabric industry:
Sustainable Sourcing and Production
Sustainability will remain a central theme in the textile industry. There is a growing emphasis on sustainable cotton farming practices, such as organic and regenerative agriculture, which reduce environmental impact and promote soil health.
Additionally, innovations in water-efficient cotton cultivation and eco-friendly dyeing processes will gain prominence.
Circular Economy
The concept of a circular economy, where products are designed for reuse, recycling, and longevity, will impact cotton fabric.
Innovations in textile recycling technologies will allow for reprocessing old cotton garments into new fabrics, reducing waste and conserving resources.
Smart Textiles
Cotton fabrics infused with technology, often called smart textiles or e-textiles, are rising.
These textiles can include sensors, conductive threads, and integrated electronics. They have applications in wearable technology, medical textiles, and even fashion.
Nanotechnology
Nanotechnology is being explored to enhance cotton fabric properties. Nanoparticles can be used to impart properties like stain resistance, UV protection, and even antibacterial qualities to cotton fabrics.
Biodegradable and Recyclable Cotton Blends
Researchers are working on developing biodegradable and recyclable cotton blends by combining cotton with other sustainable fibers such as hemp, bamboo, or lyocell.
These blends can offer improved performance and reduce the environmental footprint of textiles.
3D Printing
3D printing technology is being adapted for textile production. It allows for the creation of intricate and customized designs, reducing waste by printing textiles directly without the need for cutting and sewing.
Performance Fabrics
Innovations in cotton fabric finishing treatments will lead to performance textiles that are wrinkle-resistant, moisture-wicking, and UV-resistant. These fabrics will find applications in sportswear, activewear, and outdoor gear.
Digital Printing
Digital printing on cotton fabrics is becoming more sophisticated and accessible. This allows for highly detailed and customizable designs with reduced water and ink usage compared to traditional printing methods.
Blockchain Traceability
Concerns about the authenticity and ethical sourcing of cotton will drive the adoption of blockchain technology for supply chain transparency. Consumers will be able to trace the journey of cotton from the farm to the final product.
Innovative Textile Recycling
Advances in textile recycling technologies will make it easier to recover and reuse cotton fibers from discarded garments. This will contribute to a more closed-loop and sustainable textile industry.
Customization and Personalization
As consumer preferences for individualization grow, there will be greater demand for customized and personalized cotton fabrics. Digital printing and other technologies will enable consumers to design their own fabrics.
Inclusive Sizing and Accessibility
The fashion industry is moving towards greater inclusivity in sizing and accessibility for people with disabilities.
Cotton fabric producers must adapt to these changing demands by offering a wider range of sizes and functional features.
FAQs
What is the first step in turning cotton into fabric?
The first step is harvesting mature cotton bolls from the cotton plants.
What happens after the cotton is harvested?
After harvesting, the cotton undergoes ginning, which removes seeds and impurities from the fibers.
How are cotton fibers transformed into yarn?
After ginning, the fibers are carded to align and clean them. Then, they are spun into yarn using machines called spinning frames.
What are the main methods of turning cotton yarn into fabric?
Cotton yarn can be woven on a loom to create interlocking patterns or knitted to form a stretchy, flexible fabric.
Are there additional processes involved before cotton fabric is ready for use?
Yes, the cotton fabric may undergo dyeing, printing, and finishing treatments after weaving or knitting.
To Recap
The journey of cotton from field to fabric is a remarkable testament to human ingenuity and innovation.
Each step contributes to creating the versatile and beloved fabric, from the meticulous cultivation and harvesting of cotton bolls to the precise processes of ginning, carding, and spinning.
Weaving or knitting the spun fibers transforms them into a textile ready for dyeing, printing, and finishing. Quality control measures ensure the fabric meets high standards.
Finally, cotton becomes the clothing, textiles, and industrial materials that enrich our daily lives through cutting, sewing, packaging, and distribution. This intricate process underscores the enduring significance of cotton in our global textile industry.
Leave a Reply