Planar resin flatbacks are a fun and unique craft item that you can make at home. These flatbacks are made by printing an image onto shrink plastic and then using resin to create a glossy, 3D effect.
They are perfect for making keychains, center parts for bows, magnets, and crock charms, and can also be used for geocaching swag.
The process of making planar resin flatbacks is relatively simple and can be a great way to get creative with your crafting. In this guide, we will walk you through the materials and steps needed to make your own planar resin flatbacks.
From printing the image on shrink plastic to mixing and applying the resin, we’ll cover everything you need to know. So, let’s get started and see what you can create.
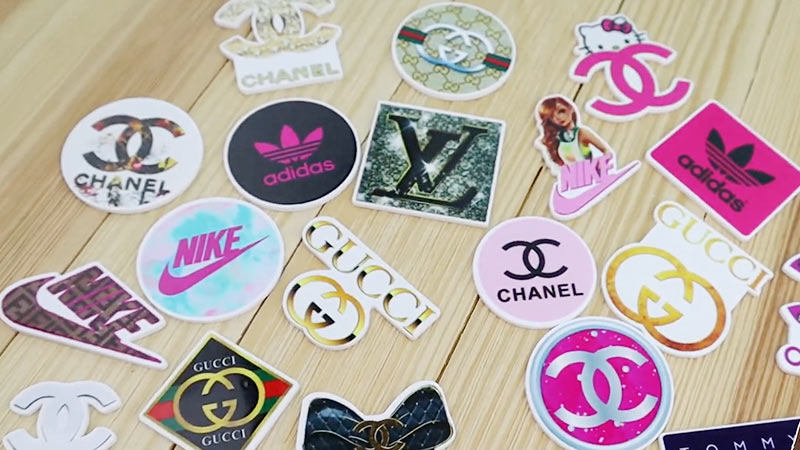
Preparing the Shrink Plastic
To print an image onto shrink plastic, you will need a printer that is compatible with the shrink plastic. You can usually find the specific instructions for printing on shrink plastic with the product or on the manufacturer’s website.
Here are some general steps to follow:
- Load the shrink plastic into the printer according to the instructions for your specific printer. This may involve feeding it through the printer manually or loading it into a tray.
- Open the image that you want to print in a graphic design or image editing software.
- Resize the image to fit the size of the shrink plastic. You can usually find the dimensions of the shrink plastic on the packaging.
- Print the image according to the instructions for your specific printer. Be sure to set the print quality to the highest setting to ensure the best possible image quality.
- Allow the ink to dry completely before moving on to the next step.
To cut out the image from the shrink plastic, you can use a pair of scissors or a craft knife. Be sure to leave a small border around the edges of the image to allow for shrinkage during the heating process.
Some tips for ensuring the best quality print on shrink plastic include:
- Use a high-quality printer and ink: The quality of the printer and ink that you use can have a big impact on the final result.
- Use graphic design or image editing software to adjust the size and resolution of the image: This will help to ensure that the image is the correct size and has the highest possible resolution.
- Avoid touching the ink with your fingers: The oils from your skin can cause the ink to smudge or smear.
- Allow the ink to dry completely before cutting out the image: This will help to prevent smudging or smearing.
Shrinking the Plastic
To shrink the plastic, follow these steps:
- Preheat your oven according to the instructions on the shrunk plastic package.
- Place your image onto a baking sheet and place it in the oven.
- Bake the image for the time specified on the shrunk plastic package. This will typically be between 1-3 minutes.
- Once the time is up, remove the baking sheet from the oven and allow the image to cool.
- Once the image has cooled, it should be shrunk to a smaller size and have a glossy finish.
Some safety tips to keep in mind when working with an oven include:
- Wear oven mitts or gloves to protect your hands from the heat.
- Keep a close eye on the image while it is in the oven to ensure that it does not burn or catch fire.
- Do not leave the oven unattended while the image is inside.
- Keep flammable materials away from the oven.
If you encounter any problems while shrinking the plastic, here are some potential solutions:
- If the image does not shrink or becomes distorted, it may be that the oven was not hot enough or that the image was left in the oven for too long. In this case, try adjusting the oven temperature or the baking time and try again.
- If the image becomes wrinkled or crinkled during the shrinking process, it may be that the plastic was not heated evenly. This can be caused by the image is too close to the sides or bottom of the oven, or by the image being too thick. To fix this issue, try moving the image to a more central location in the oven or using thinner shrink plastic.
- If the image sticks to the baking sheet or becomes stuck to itself, it may be that the plastic was not cooled properly before being removed from the oven. To fix this issue, try allowing the image to cool completely before attempting to remove it from the baking sheet.
Mixing and Pouring the Resin
To mix the resin, follow the instructions provided in the package. Here are some general steps to follow:
- Gather all of the necessary materials and equipment, including the resin, hardener, mixing cups, stirring sticks, and any protective gear (such as gloves and safety glasses).
- Read the instructions on the package carefully and follow all of the safety precautions.
- Measure out the appropriate amounts of resin and hardener according to the instructions on the package.
- Pour the resin and hardener into a mixing cup.
- Using a stirring stick, mix the resin and hardener together according to the instructions on the package. This may involve stirring for a certain amount of time or until the mixture reaches a specific consistency.
- Once the resin is mixed, you are ready to pour it into the silicone dome mold.
To pour the resin into the silicone dome mold, follow these steps:
- Place the silicone dome mold onto a flat, stable surface.
- Slowly and carefully pour the resin into the mold, filling it to the desired level.
- Tap the mold gently to remove any air bubbles that may have formed.
- Allow the resin to sit for a few minutes to allow any remaining air bubbles to rise to the surface.
- Once the resin is smooth and bubble-free, you are ready to assemble the flatback.
It is important to take safety precautions when working with resin, as it can be harmful if inhaled or ingested. Some precautions to take include:
- Wear protective gear, such as gloves and safety glasses.
- Work in a well-ventilated area.
- Do not eat or drink while working with resin.
- Keep children and pets away from the resin.
- Follow the specific instructions and precautions provided on the resin package.
Assembling the Flatback
To assemble the flatback, follow these steps:
- Place the shrink plastic image onto the resin-filled silicone dome mold.
- Press the image down gently to ensure that it is fully submerged in the resin.
- Use a toothpick or pin to smooth out any air bubbles or imperfections on the surface of the resin.
- Allow the resin to sit for a few minutes to allow any remaining air bubbles to rise to the surface.
- Once the resin is smooth and bubble-free, you are ready to move on to the curing process.
To ensure that the image is fully submerged in the resin, it can be helpful to use a small object (such as a paper clip or pin) to gently hold the image in place while the resin sets. You can also use a toothpick or pin to gently push any air bubbles or imperfections to the edges of the mold.
If you are having trouble getting the image to stay submerged in the resin, it may be helpful to try using a heavier object (such as a paperweight) to hold the image down. Alternatively, you can try adding more resin to the mold to ensure that the image is fully covered.
Curing the Resin
The curing process for resin refers to the time it takes for the resin to harden and set into its final form. The amount of time that it takes for the resin to cure will depend on the specific type of resin that you are using, as well as the ambient temperature and humidity. It is important to follow the instructions on the resin package for the recommended curing time and any special considerations.
To cure the resin, follow these steps:
- Allow the resin to sit undisturbed in a well-ventilated area until it is fully cured.
- Avoid touching or moving the resin while it is curing, as this can cause it to become distorted or damaged.
- Check the resin periodically to ensure that it is curing properly.
If you encounter any issues while the resin is curing, here are some potential solutions:
- If the resin is not curing properly, it may be due to the ambient temperature or humidity being too high or too low. In this case, try moving the resin to a different location or adjusting the temperature or humidity as needed.
- If the resin is not curing evenly, it may be due to the resin being too thick or not mixed thoroughly enough. To fix this issue, try adding a thinner layer of resin or mixing the resin more thoroughly before pouring it into the mold.
- If the resin becomes distorted or bubbly during the curing process, it may be due to the resin being subjected to too much heat or movement. To fix this issue, try keeping the resin in a stable, undisturbed location and avoid exposing it to heat or movement.
- If the resin becomes discolored or yellowed during the curing process, it may be due to the resin reacting to UV light or other environmental factors. To fix this issue, try curing the resin in a location with less UV exposure or using a UV-protective coating on the resin.
Removing the Flatback From the Mold
To remove the flatback from the mold, follow these steps:
- Wait until the resin is fully cured before attempting to remove the flatback from the mold. This will typically take several hours or up to a few days, depending on the specific type of resin that you are using.
- Carefully lift the silicone mold off of the flatback.
- Gently peel the silicone mold away from the flatback, starting at the edges and working your way inward.
- If the flatback is stuck to the mold, you can try gently prying it off with a toothpick or pin. You can also try carefully heating the mold with a heat gun or blow dryer to soften the resin and make it easier to remove.
To avoid damaging the flatback, it is important to be gentle and take your time when removing it from the mold. Be sure to handle the flatback by the edges to avoid leaving fingerprints or smudges on the surface. If you are having trouble removing the flatback from the mold, it may be helpful to gently bend or flex the mold to loosen the resin.
Finishing Touches
Once the flatback has been removed from the mold, you may wish to take some additional steps to finish it.
Here are some options to consider:
- Sanding: If the edges of the flatback are rough or uneven, you can use sandpaper to smooth them out. Be sure to use fine-grit sandpaper and sand gently to avoid damaging the surface of the resin.
- Protective coating: If you want to add an extra layer of protection to the flatback, you can apply a clear nail polish or resin sealant to the surface. This will help to protect the resin from scratches and other damage.
- Decorative elements: You can add some extra flair to your flatback by adding decorative elements such as glitter, beads, or other small embellishments. Simply mix the decorative elements into the resin before pouring it into the mold, or glue them onto the surface of the flatback after it has been removed from the mold.
There are many creative ways to use finished flatbacks in crafting projects. Some ideas include:
- Keychains: Attach a keyring or jump ring to the flatback to create a unique and personalized keychain.
- Centerpieces for bows: Use the flatback as the centerpiece for a handmade hair bow or headband.
- Magnets: Glue a magnet to the back of the flatback to create a customizable magnet for your fridge or office.
- Crock charms: Attach a lobster clasp or jump ring to the flatback to create a charm for your crock pot or kitchen utensils.
- Jewelry: Use the flatback to create earrings, pendants, or other pieces of jewelry.
- Ornaments: Hang the flatback from a ribbon
Comparison of Resin Types for Planar Resin Flatbacks
Here is a comparison table that highlights the differences between different types of resin commonly used for making planar resin flatbacks:
Resin Type | Characteristics |
---|---|
Epoxy resin | Strong and durable, resistant to water and chemicals, requires careful mixing, can yellow over time |
Urethane resin | Flexible and resistant to impact, resistant to water and chemicals, requires precise measuring, may have strong odor |
Acrylic resin | Low-cost and easy to use, water-soluble, dries clear and hard, may yellow or become brittle over time |
FAQs
Yes, you can use any type of image that you like for the shrink plastic. This can include photographs, illustrations, text, or any other design that you want to create. Keep in mind that the image will shrink down to a smaller size once the plastic is heated, so you may need to adjust the size of the image accordingly.
Yes, you can use a variety of different types of resin for this project. Some options include epoxy resin, urethane resin, or acrylic resin. Each type of resin has its own specific properties and characteristics, so be sure to choose the one that is best suited to your project.
Yes, you can use a variety of different types of molds for this project. Some options include silicone molds, plastic molds, or even hand-crafted molds made out of clay or other materials. Keep in mind that the size and shape of the mold will affect the final size and shape of the flatback, so choose a mold that is appropriate for your project.
Yes, you can add color to the resin to create a wide range of effects. Some options include using resin dyes, pigment powders, or acrylic paints. Simply mix the colorant into the resin according to the instructions on the package or the specific product that you are using.
In general, it is not recommended to use resin flatbacks for outdoor projects as they are not waterproof and may become damaged by exposure to the elements. If you do want to use the flatbacks for an outdoor project, it is important to protect them from direct exposure to moisture and UV light by using a waterproof sealant or UV-protective coating.
Conclusion
Making a planar resin flatback is a fun and creative crafting project that allows you to create customized, one-of-a-kind pieces.
By following the steps outlined in this tutorial and choosing the right materials and tools, you can create your own resin flatbacks for use in a variety of projects.
Whether you are a seasoned resin crafter or new to the medium, there are many options available for creating unique and eye-catching flatbacks. With a little bit of creativity and some basic supplies, the possibilities are endless.
Leave a Reply