The world of textiles is woven with diverse techniques, each yielding fabrics with distinct characteristics. Warp knitting and circular knitting stand as two prominent methods, each bearing its unique hallmarks.
Warp knitting involves using separate yarns to craft intricate textures, while circular knitting employs a continuous yarn to create seamless tubes. These techniques play a pivotal role in shaping fabrics’ strength, stretch, and design complexity.
In the following exploration, we delve into the 20 key differences between these methods, shedding light on their production processes, fabric properties, applications, and more.
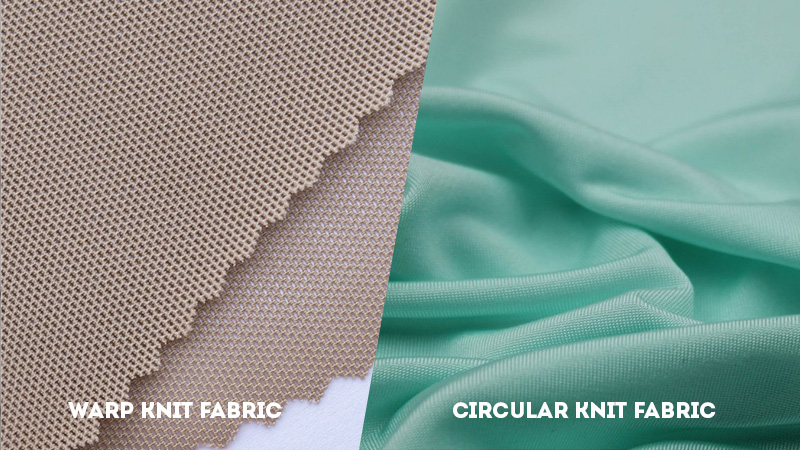
Key Differences Between Warp Knit and Circular Knit
Method of Production
- Warp Knit: Warp knitting involves a unique method of production where each stitch is created using a separate yarn from the warp direction. Specialized warp knitting machines are used for this process. The yarns are threaded through the machine’s needles, and multiple yarns work in tandem to produce parallel columns of loops.
- Circular Knit: In contrast, circular knitting employs a continuous yarn that forms loops in a spiral or circular manner. Whether using circular knitting machines or hand-knitting techniques, this approach creates a seamless tube, eliminating the need for complex stitching. The method is often chosen for its efficiency and ease of producing seamless garments and products.
Seamlessness
- Warp Knit: The seamlessness of warp-knitted fabrics depends on the specific pattern and machine settings. While some warp knits can be seamless, others may require stitching together multiple panels, leading to potential seams. This variation arises due to the flexibility in warp knitting machine configurations.
- Circular Knit: Circular knitting inherently yields seamless tubes, making it ideal for producing garments that require continuous, uninterrupted fabric, like socks, hats, and tube-shaped apparel. The circular knitting process ensures that there are no seams, enhancing both comfort and aesthetic appeal.
Fabric Characteristics
- Warp Knit: Fabrics resulting from warp knitting are known for their stability and strength. They possess less stretch compared to circular-knit fabrics and exhibit high strength along the warp direction. This makes them suitable for applications where durability and stability are crucial, such as lingerie, swimwear, and technical textiles.
- Circular Knit: Circular-knitted fabrics are characterized by their elasticity and stretchability. They are capable of stretching and recovering without losing their shape. This elasticity makes them popular for garments that require flexibility and comfort, such as activewear, T-shirts, and knitwear.
Yarn Usage
- Warp Knit: In warp knitting, the use of multiple yarns for each stitch creates a unique texture and structure. The individual yarns are threaded through separate needles to create parallel columns of loops, resulting in a distinctive appearance in the fabric.
- Circular Knit: Circular knitting employs a single continuous yarn that loops around the needles to form the fabric. This approach simplifies the production process, as only one yarn is used to create the entire fabric. The resulting fabric has a more uniform texture compared to warp-knitted fabrics.
Complexity of Design
- Warp Knit: Warp knitting machines can be configured to produce a wide range of intricate patterns and designs. The ability to control multiple yarns individually allows for the creation of lace-like fabrics, elaborate textures, and complex structures.
- Circular Knit: While circular knitting can achieve some variations in stitches and patterns, its design complexity is generally simpler than that of warp knitting. The continuous loop formation limits the types of patterns that can be created. As a result, circular knitting is often chosen for producing garments with straightforward designs and textures.
Production Speed
- Warp Knit: The production speed of warp knitting is typically slower compared to circular knitting. This is due to the complexity of handling multiple yarns individually. The process of threading and controlling these multiple yarns requires precision and can lead to a slower overall production pace.
- Circular Knit: Circular knitting is generally faster in terms of production speed. The use of a single continuous yarn simplifies the knitting process, resulting in a more efficient and continuous workflow. This advantage makes circular knitting suitable for large-scale production.
Stretchiness
- Warp Knit: Warp-knitted fabrics have limited stretchiness compared to circular-knitted fabrics. The parallel columns of loops formed by the separate yarns in warp knitting contribute to a fabric structure that offers less elasticity and stretch recovery.
- Circular Knit: Circular-knitted fabrics are renowned for their high elasticity and excellent stretch recovery. The continuous loop formation of the fabric structure allows it to stretch and regain its original shape, making it suitable for garments that require flexibility and ease of movement.
Applications
- Warp Knit: Warp knitting finds applications in various products that demand stability and strength. Fabrics produced through warp knitting are used in lingerie, swimwear, upholstery, technical textiles, and other items where durability and specific textures are important.
- Circular Knit: Circular knitting is versatile and well-suited for a wide range of applications. It is commonly used to create seamless garments, including T-shirts, sweaters, socks, and hosiery. The stretchiness of circular-knitted fabrics makes them popular for activewear and other apparel requiring comfort and flexibility.
Strength
- Warp Knit: Warp-knitted fabrics excel in terms of strength, especially in the warp direction. The parallel arrangement of yarns contributes to their enhanced tensile strength, making them suitable for applications where fabric durability is critical.
- Circular Knit: Circular-knitted fabrics offer balanced strength in both the lengthwise and crosswise directions. While they may not exhibit the same level of strength as warp-knitted fabrics in the warp direction, their overall strength is sufficient for most clothing and textile applications.
Needle Configuration
- Warp Knit: The needle configuration for warp knitting machines is complex, as each yarn requires its own set of needles. This complexity arises from the need to manipulate multiple yarns simultaneously to create the desired fabric structure.
- Circular Knit: Circular knitting involves a simpler needle configuration. The continuous loop formation only requires a single yarn to be threaded through the needles, simplifying the mechanics of the knitting process. This simplicity contributes to the efficiency and speed of circular knitting.
Production Scale
- Warp Knit: Warp knitting is often favored for large-scale production due to its ability to create fabrics with intricate patterns and textures efficiently. Despite its slower individual stitch creation, the advanced technology of modern warp knitting machines allows for high-speed production of a wide range of textile products.
- Circular Knit: Circular knitting is adaptable to both small and large-scale production. While its individual stitch creation process is faster than warp knitting, the simplicity of the technique makes it well-suited for producing garments in varying quantities.
Fabric Texture
- Warp Knit: Warp-knitted fabrics offer diverse texture possibilities. The intricate manipulation of multiple yarns in warp knitting machines allows for the creation of complex textures, laces, and patterns that result in unique and visually appealing fabrics.
- Circular Knit: Circular-knitted fabrics tend to have a smoother and more uniform texture compared to warp-knitted fabrics. While variations in stitch patterns are possible, the continuous loop formation of circular knitting limits the level of texture complexity achievable.
Joining Panels
- Warp Knit: In warp knitting, fabrics can sometimes require joining panels together to achieve the desired size. This process involves stitching separate panels, which may lead to visible seams and extra production steps.
- Circular Knit: Circular knitting inherently creates seamless tubes due to its continuous loop formation. This eliminates the need for joining panels and produces a seamless, more aesthetically pleasing result.
Yarn Tension
- Warp Knit: Achieving proper tension for multiple yarns in warp knitting can be intricate. Each yarn requires individual tension adjustments to ensure consistent stitch quality and fabric appearance.
- Circular Knit: Circular knitting involves simpler yarn tension control since it uses a single continuous yarn. This reduces the complexity of managing tension compared to warp knitting.
Raw Material Handling
- Warp Knit: Warp knitting requires the handling of multiple yarns, which can be more complex in terms of feeding, threading, and controlling tensions. This can lead to increased setup time and potential challenges in maintaining uniformity.
- Circular Knit: Circular knitting simplifies raw material handling as it involves only one continuous yarn. This ease of handling contributes to a streamlined production process and efficient material usage.
Durability
- Warp Knit: Warp-knitted fabrics are often more durable due to their higher tensile strength, particularly in the warp direction. This durability makes them suitable for applications that require resistance to wear and tear, such as upholstery, technical textiles, and items subjected to heavy use.
- Circular Knit: While circular-knitted fabrics are generally durable, their higher stretchiness and elasticity might lead to slightly less overall durability compared to warp-knitted fabrics. However, their stretch recovery properties contribute to maintaining their shape over time.
Stretch Recovery
- Warp Knit: Warp-knitted fabrics have lower stretch recovery due to their inherent structure. The parallel arrangement of yarns can limit the fabric’s ability to bounce back to its original shape after being stretched.
- Circular Knit: Circular-knitted fabrics excel in stretch recovery. The continuous loop formation enables the fabric to retain its shape even after being stretched, ensuring that garments maintain their fit and appearance.
Cost Efficiency
- Warp Knit: Warp knitting can be more resource-intensive in terms of yarn consumption due to the use of multiple yarns for each stitch. This can contribute to higher production costs, especially for intricate patterns.
- Circular Knit: Circular knitting is generally more cost-efficient in terms of yarn usage. The use of a single continuous yarn simplifies material consumption and contributes to overall cost savings, making it a practical choice for large-scale production.
Stability
- Warp Knit: Warp-knitted fabrics tend to offer greater stability due to their fabric structure and the arrangement of multiple yarns. This stability makes them well-suited for products that require structural integrity and resistance to distortion.
- Circular Knit: Circular-knitted fabrics have a circular structure, which can lead to slightly less stability compared to warp-knitted fabrics. However, this does not necessarily impede their suitability for various applications.
Suitable Products
- Warp Knit: Warp knitting is ideal for products where strength, structure, and unique textures are paramount. This includes lace, lingerie, swimwear, and technical textiles where the fabric’s physical attributes are critical.
- Circular Knit: Circular knitting is well-suited for products that demand stretch, comfort, and seamless construction. Garments like T-shirts, sweaters, socks, and activewear benefit from the elasticity and ease of production associated with circular knitting.
Machine Complexity
- Warp Knit: The machinery used for warp knitting is often more complex due to the need to handle multiple yarns simultaneously and create intricate patterns. Specialized warp knitting machines are required to achieve the desired fabric outcomes.
- Circular Knit: Circular knitting machines are generally less complex compared to warp knitting machines. Their simpler design and operation contribute to easier maintenance, setup, and operation, making them suitable for a broader range of applications.
Warp Knit Vs Circular Knit: Comparison Table
Aspect | Warp Knit | Circular Knit |
---|---|---|
Method of Production | Uses separate yarns for each stitch from warp. | Utilizes a single continuous yarn in a circular path. |
Seamlessness | Can be either seamless or seamed depending on pattern. | Inherently creates seamless tubes. |
Fabric Characteristics | Stable, less stretchy, high strength in warp direction. | Elastic, good stretch and recovery properties. |
Yarn Usage | Multiple yarns create parallel columns of loops. | Single continuous yarn forms loops spirally. |
Complexity of Design | Can produce intricate patterns and textures. | Tends to produce simpler and more uniform fabrics. |
Production Speed | Generally slower due to multiple yarn handling. | Generally faster due to continuous yarn. |
Stretchiness | Less elastic, limited stretch and recovery. | High elasticity, good stretch and recovery. |
Applications | Lingerie, swimwear, technical textiles. | T-shirts, sweaters, activewear, seamless garments. |
Strength | Higher strength in warp direction. | Balanced strength in both directions. |
Needle Configuration | More complex needle setup for each yarn. | Simpler needle setup for a single yarn. |
Production Scale | More suitable for large-scale production. | Flexible for both small and large-scale production. |
Fabric Texture | Various textures and patterns can be achieved. | Generally smoother and more consistent texture. |
Joining Panels | Multiple panels may require seaming. | Seamless tube creation avoids panel joining. |
Yarn Tension | Yarns need individual tension adjustments. | Single yarn tension is easier to control. |
Raw Material Handling | More complex handling of multiple yarns. | Simpler handling with a single yarn. |
Durability | Often more durable due to warp strength. | Slightly less durable due to higher elasticity. |
Stretch Recovery | Lower stretch recovery due to warp structure. | Good stretch recovery maintains shape. |
Cost Efficiency | More yarn consumption can lead to higher costs. | Generally more cost-efficient due to single yarn. |
Stability | Greater stability in fabric structure. | Slightly less stable due to circular structure. |
Suitable Products | Lace, upholstery, technical fabrics. | Seamless garments, hosiery, knitwear. |
Machine Complexity | Requires specialized warp knitting machines. | Uses circular knitting machines or hand knitting. |
Frequently Asked Questions
Yes, circular-knitted fabrics can be used for technical applications. While they might not have the same level of warp-knitted fabric’s inherent strength, their durability can still be suitable for many technical textiles, especially when combined with appropriate yarn choices and fabric constructions.
Not necessarily. While warp knitting can be slower due to the handling of multiple yarns, modern warp knitting machines equipped with advanced technology can significantly enhance production speed. Circular knitting’s advantage in speed should be weighed against the unique characteristics each technique offers.
Circular knitting is generally better suited for simpler and more uniform textures. While it’s challenging to replicate intricate lace-like patterns directly using circular knitting, innovative techniques such as combining circular knitting with other methods might achieve similar effects.
Yes, some warp-knitted fabrics can be seamless, depending on the machine settings and specific patterns used. Innovations in warp knitting technology have led to the development of seamless warp-knitted fabrics, though circular knitting remains more widely recognized for its inherent seamlessness.
Yes, circular knitting machines can produce fabrics with different levels of stretchiness by adjusting the tension of the continuous yarn and the knitting pattern. Variations in stitch type and yarn choice allow for customization of stretch and recovery properties in the resulting fabric.
To Recap
The differences between warp knitting and circular knitting emerge as crucial threads. These techniques, while distinct, intertwine to create a diverse array of fabrics tailored to specific needs.
From the seamless perfection of circular knit to the intricate textures of warp knit, each approach brings unique strengths to the textile industry.
Understanding these differences empowers designers, manufacturers, and enthusiasts to make informed choices, ensuring that the fabrics they create meet the desired standards of aesthetics, functionality, and performance.
The interplay of these techniques continues to shape the evolving landscape of textile innovation.
Leave a Reply