A chart or graph sewing pattern in crochet or knitting is a visual blueprint that translates intricate designs into a symbolic language of stitches and rows.
Using symbols or colors, these charts offer crafters a graphical representation of patterns, enabling them to envision and implement complex designs precisely.
Commonly accompanied by a key, these charts decode the symbols or colors, functioning as an indispensable visual guide for stitch placement and pattern comprehension.
Stitch charts, color charts, and symbol charts are pivotal tools in the crafting repertoire, working in tandem with written instructions to empower artisans in transforming yarn into beautifully patterned and meticulously crafted projects.
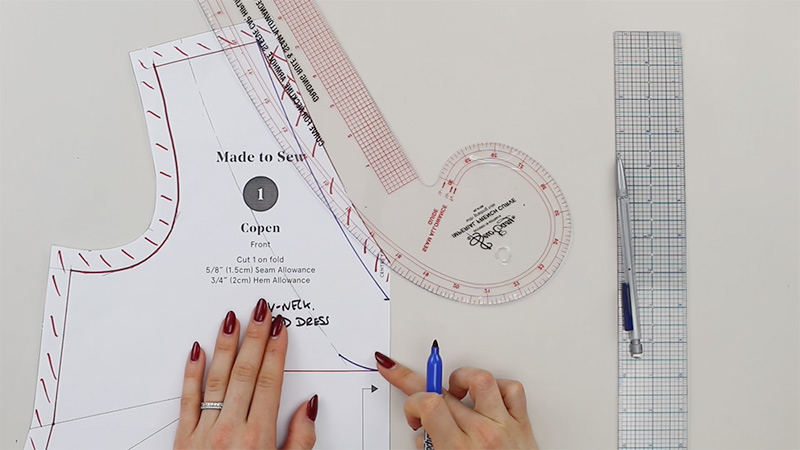
What Is a Chart or Graph Sewing Pattern?
A chart or graph sewing pattern in the context of crochet or knitting serves as a visual roadmap for crafters, offering a clear and concise representation of a pattern’s intricacies.
Typically composed of symbols or colors, these charts provide a bird’s-eye view of each stitch and row, aiding in project visualization.
Crafters utilize them to design intricate patterns or execute complex techniques with precision. The charts may focus on specific project segments, accompanied by a key that elucidates the meaning of each symbol or color.
Stitch, color, and symbol charts are the primary types used in these patterns. Stitch charts visually map out the sequence of stitches, guiding the crafter on where to place each one.
Color charts, on the other hand, use colors to represent different yarn shades or types of stitches, enhancing clarity.
Symbol charts employ symbols to denote specific stitches or actions, contributing to a universal crafting language.
These charts often complement written instructions, providing comprehensive guidance for crochet and knitting enthusiasts.
Uses of Patterns in Garment Construction
Patterns play a crucial role in garment construction, serving as the blueprint or template that guides the assembly of fabric pieces into a finished garment.
The creation and utilization of patterns are essential in achieving precision, consistency, and efficiency in the production process.
Here are some key uses of patterns in garment construction:
Size and Fit Consistency
Patterns are meticulously crafted based on standardized measurements, ensuring that garments produced across different sizes maintain a consistent fit.
This is crucial for brands engaged in mass production, as it allows manufacturers to meet specific size requirements and satisfy customer expectations.
Well-established patterns help create a reliable sizing structure, promoting customer satisfaction and brand loyalty by delivering garments that consistently align with the intended fit and proportions.
Design Replication
Patterns serve as the blueprint for accurately replicating designers’ visions. A precisely drafted pattern becomes a reference point for recreating specific styles or silhouettes, preserving the integrity of a brand’s identity.
Design replication is vital for maintaining a cohesive aesthetic across collections and seasons, ensuring each garment aligns with the original design concept.
By relying on patterns, designers can efficiently translate their creative vision into tangible, market-ready products.
Efficiency in Production
Efficiency in garment production is significantly enhanced through the use of patterns. These templates streamline the cutting and sewing processes, leading to increased productivity.
With well-defined patterns, fabric pieces can be cut with minimal waste, making assembly more systematic and time-effective.
This efficiency is particularly advantageous for large-scale manufacturing, where optimizing resources and reducing production time are essential for meeting market demands and staying competitive.
Customization and Tailoring
Patterns play a pivotal role in custom tailoring and smaller-scale production. Tailors utilize patterns as a starting point, adapting them to individual measurements and preferences.
This customization ensures a perfect fit and creates bespoke garments tailored to each customer’s unique needs and tastes.
Patterns serve as the foundation for craftsmanship, providing a framework that can be personalized to bring a client’s vision to life while maintaining structural integrity.
Reproducibility
The reproducibility of a garment is made possible through the development and utilization of patterns.
Once a pattern is meticulously crafted and tested, it becomes a reliable tool for producing multiple copies of the same design.
This is crucial for designers and manufacturers aiming to create cohesive collections or fulfill bulk orders with consistent quality.
Patterns contribute to the scalability of production, enabling the replication of successful designs without compromising precision or uniformity.
Cost Control
Precise patterns are instrumental in controlling costs throughout the garment production process. Manufacturers can reduce material costs by optimizing fabric usage and minimizing waste during cutting.
Additionally, the streamlined production processes facilitated by patterns contribute to overall cost-effectiveness.
This dual impact on material and operational efficiency makes precise patterns indispensable for maintaining competitiveness in the fashion industry.
Communication Tool
Patterns serve as a universal language in garment construction, communicating between designers, patternmakers, and production teams.
They convey essential information about garment construction, including seam placements, grain lines, and notches.
This ensures that everyone involved in the production process clearly understands how the garment should be assembled, promoting seamless collaboration and minimizing errors in interpretation.
Innovation and Experimentation
Patterns provide a solid foundation for innovation and experimentation in garment design. Designers can use established patterns as a starting point to explore various alterations, unconventional techniques, and unique variations.
This allows for creating avant-garde and distinctive fashion pieces, pushing the boundaries of traditional design and fostering creativity within the industry.
Patterns serve as a springboard for designers to express their artistic vision and bring fresh, cutting-edge concepts to the fashion landscape.
Types of Graph Patterns for Sewing
In sewing and garment construction, graph patterns, also known as sewing patterns, are templates that guide the cutting and assembling of fabric pieces to create a finished garment.
These patterns come in various types, each serving specific purposes and catering to different styles and complexities of clothing.
Here are the common types of graph patterns used in sewing:
Commercial Patterns
Commercial sewing patterns are a staple for home sewers, offering designs from established pattern companies.
Designed for various skill levels, these patterns cater to the needs of those new to sewing and seasoned enthusiasts alike.
With detailed instructions and multiple size options, commercial patterns provide a reliable starting point for creating dresses, tops, bottoms, and accessories.
They serve as an accessible and user-friendly resource, guiding sewers through each construction process step.
PDF Patterns
In the digital age, PDF patterns have gained popularity as downloadable files that users can print at home.
These patterns, often created by independent designers, offer instant accessibility without the need for physical shipping.
PDF patterns come with detailed instructions and frequently encompass various sizes, making them versatile for multiple body types.
The convenience of instant access and the flexibility of size options make PDF patterns attractive for modern sewers.
Custom-Fitted Patterns
Custom-fitted patterns represent the pinnacle of personalized garment creation. Tailored to an individual’s precise measurements, these patterns are commonly used in bespoke tailoring and made-to-measure clothing.
Crafting such patterns involves a meticulous process of taking detailed measurements from the wearer, ensuring a perfect fit that complements the unique contours of their body.
Although custom-fitted patterns demand more time and expertise, the result is a garment distinctly tailored to the individual’s body shape, providing unparalleled comfort and style.
Vintage Patterns
Vintage patterns evoke the charm and nostalgia of fashion from bygone eras. They can be authentic finds from the past or reproductions inspired by historical styles.
Vintage patterns often showcase unique design elements reflective of specific decades, allowing sewers to recreate authentic looks from times gone by.
Perfect for enthusiasts of retro or historical fashion, vintage patterns offer a creative journey into the rich tapestry of fashion history.
Designer Patterns
Designer patterns bring a touch of high fashion to the home sewing realm. Created in collaboration with well-known designers, these patterns allow sewers to replicate runway looks at a more affordable price.
Designer patterns often feature intricate design details and advanced construction techniques, making them suitable for sewers with intermediate to advanced skills.
By offering a taste of the latest trends, designer patterns enable home sewers to infuse their wardrobes with couture.
Knit Patterns
Knit patterns cater specifically to the unique characteristics of stretchy knit fabrics. Designed for materials like jersey and interlock, these patterns ensure that the finished garment is stylish, comfortable, and capable of retaining its shape.
Common knit patterns include wardrobe staples like T-shirts, leggings, and dresses. The emphasis on accommodating stretch makes these patterns ideal for creating garments that seamlessly blend style with ease of movement.
Children’s Patterns
Children’s patterns address the specific proportions and needs of young wearers. These scaled-down versions of adult patterns cover a range of garments suitable for different ages and occasions.
Children’s patterns often incorporate features such as adjustable sizing to accommodate growth, making them practical for parents and caregivers looking to create clothing that can adapt to a child’s changing body.
Lingerie and Swimwear Patterns
Specialized patterns for lingerie and swimwear cater to the intricate construction of intimate apparel.
These patterns may include features like underwire support, elastic applications, and detailed instructions for working with delicate fabrics like lace and silk.
Ideal for sewers looking to explore the world of undergarment creation, lingerie, and swimwear patterns provide the necessary guidance to achieve a comfortable and stylish fit in these specialized garments.
Types of Pattern Making in Clothing
Pattern making in clothing is a crucial step in the garment production process, involving the creation of templates that guide the cutting and assembly of fabric pieces.
Pattern-making techniques produce patterns tailored to different styles, fits, and design elements.
Here are the common types of pattern-making in clothing:
Flat Pattern Making
Flat pattern making is a meticulous process that involves translating a garment design onto a two-dimensional surface.
Pattern makers use precise measurements and mathematical calculations to draft patterns directly onto paper or cardboard.
This method is celebrated for its precision and efficiency, making it a cornerstone in the fashion industry.
Adjustments are made during the drafting process to accommodate design elements, achieve the desired fit, and capture the intended style.
Flat pattern-making allows for a systematic approach to creating templates that are the foundation for garments, ensuring consistency and accuracy in mass production.
Draping or Draped Pattern Making
Draping, or draped pattern making, is a hands-on, tactile approach where fabric is directly manipulated on a dress form or mannequin.
This technique provides a unique opportunity for pattern makers to visualize and experiment with the fabric’s drape, flow, and structure.
Commonly employed in high-end fashion and couture, draping allows for an intuitive and creative design process.
Pattern makers can make immediate adjustments, exploring various silhouettes and design details in real time, resulting in garments that showcase a refined sense of craftsmanship and artistry.
Drafting
Drafting is a fundamental pattern-making technique that creates patterns from scratch using precise measurements and basic geometric shapes.
Pattern makers employ tools such as rulers and curves to draw lines and curves directly onto paper or drafting paper. This versatile method forms the basis for many other pattern-making techniques.
Drafting allows for creating unique patterns tailored to specific design requirements, providing pattern makers with the flexibility to bring diverse concepts to life.
Grading
Grading is a systematic process ensuring a design maintains its proportions and fit across various size ranges.
Grading rules are applied to the original pattern, systematically increasing or decreasing dimensions to generate larger or smaller sizes while preserving the design’s integrity.
This technique is crucial for achieving size consistency in mass production, accommodating the intended consumer base’s diverse body shapes and proportions.
Computer-Aided Design (CAD)
Computer-aided design (CAD) technology has revolutionized pattern-making by introducing a digital approach. Pattern makers use CAD systems to create, modify digitally, and store patterns.
CAD technology’s precision and flexibility enable quick adjustments and iterations, fostering efficient collaboration between designers and pattern makers.
This digital method enhances communication throughout the garment production process, streamlining workflows and providing a platform for design and pattern creation innovation.
Knitwear Pattern Making
Knitwear pattern-making is a specialized technique for garments made from stretchy knit fabrics. Unlike woven fabrics, knit fabrics require patterns that account for stretch and recovery.
Pattern makers consider ease, negative ease, and stitch patterns to create templates suitable for sweaters, T-shirts, and leggings.
This technique ensures that knitwear garments fit well and provide the necessary comfort and flexibility inherent to stretch fabrics.
Block Pattern Making
Block pattern making, also known as slopers, involves developing basic templates that serve as a starting point for creating more complex designs.
Pattern makers create foundational blocks for different garment types, such as bodice and sleeve blocks, which can be customized and adapted for various styles.
Block patterns provide a standardized foundation, facilitating efficient design development while maintaining consistency and accuracy.
Modular Pattern Making
Modular pattern-making introduces a versatile approach by creating patterns in modular or interchangeable sections. Pattern makers can mix and match these modular components to generate diverse designs.
This approach is beneficial for designers and brands aiming to create cohesive collections using a set of interchangeable elements.
Modular pattern-making fosters creativity and flexibility in design while optimizing efficiency in the pattern development process.
Adaptation from Existing Patterns
Pattern makers often adapt existing patterns as a time-saving approach, especially when working within a specific aesthetic or brand identity.
This involves modifying style lines, adding or removing design elements, or adjusting fit based on the requirements of a new design.
Adapting existing patterns allows for efficiency in pattern development while still providing the creative freedom to bring fresh perspectives to familiar templates.
Experimental or Creative Pattern Making
Experimental pattern-making encourages pattern-makers to push the boundaries of traditional techniques, fostering avant-garde and innovative designs.
This approach involves exploring unconventional methods, manipulating fabric uniquely, and experimenting with non-traditional pattern shapes.
Pattern makers engage in a creative and exploratory process to achieve cutting-edge and artistic garments that challenge conventional notions of design and construction.
This type of pattern-making emphasizes creativity, experimentation, and the pursuit of unique and distinctive fashion statements.
FAQs
What Does Sels Mean on a Sewing Pattern?
“Sels” on a sewing pattern stands for “Selvage,” indicating the recommended direction to align the fabric edges during cutting to ensure optimal grainline placement.
How does a chart or graph sewing pattern differ from traditional written instructions?
Unlike traditional written instructions, a chart or graph sewing pattern relies on visual symbols, diagrams, and illustrations to convey information about cutting, stitching, and assembling fabric pieces.
To Recap
The chart or graph sewing pattern is an invaluable tool in the crochet and knitting world, elevating the crafting experience to new levels of precision and creativity.
As a visual roadmap, these charts empower enthusiasts to bring intricate designs to life, offering a comprehensive and intuitive guide.
The symbiotic relationship between charts and written instructions ensures clarity and accessibility for crafters of varying skill levels.
This visual language transcends barriers, whether in stitch charts, color charts, or symbol charts, fostering a shared understanding among the crafting community.
With its ability to demystify complex patterns, the chart or graph sewing pattern emerges as an indispensable companion, transforming yarn into works of art.
Leave a Reply