You have ever wondered, “What is hemming?” when it comes to sewing? Let me shed some light on this widely-used term.
Essentially, a hem in sewing refers to the finished edge of a piece of fabric. It’s the part that keeps your clothes from unraveling and gives them a polished look.
When creating garments or other products with fabric, one of the final steps is often to hem clothes. This process involves folding over the raw edge of your material and stitching it down, which prevents fraying and adds a clean finish to your project.
But how do you sew a hem? You’ll be glad to know there are several methods for doing so, depending on the garment or textile product you’re working on.
While hems in clothing might seem minor details, they play an essential role in function and fashion!
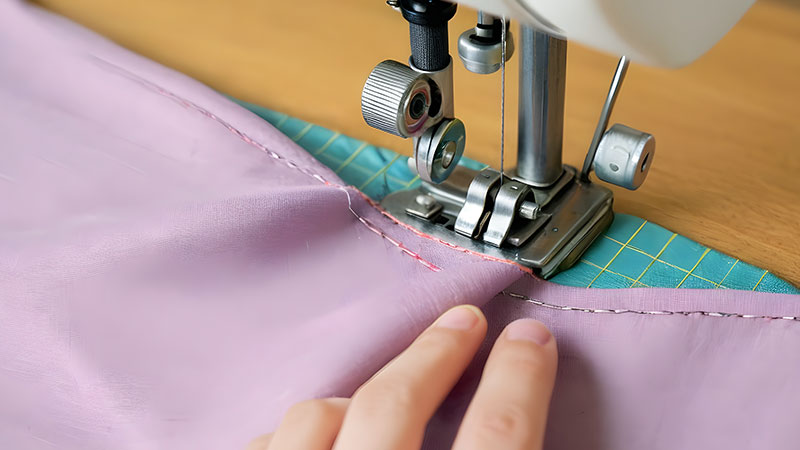
What Is a Hem in Sewing?
Diving right into the heart of sewing, let’s talk about hems. So, what is hemming? It’s a method used to neatly finish off the edges of fabric pieces, primarily on clothing items. It keeps your clothes from fraying and adds a clean, professional touch to your sewing projects.
Hemming clothes involves folding up the edge of the fabric (usually towards the inside) and stitching it down. This may sound simple, but there’s more than meets the eye.
Several types of hems can be used depending on the garment type, fabric material, or even personal preference!
A hem in clothing isn’t just functional – it also plays an aesthetic role. Their type and quality can significantly impact how a garment hangs or fits.
Some common types include rolled hems used for lightweight fabrics like silk or chiffon; double folded hems for most medium weight fabrics; and blind hems virtually invisible from the outside.
So, how do you sew a hem? The process varies slightly with each type but generally involves measuring and marking your desired length, folding and pressing the fabric, then using either hand or machine stitches to secure it.
Here’s why understanding what is a hem matters: Not only does it improve your sewing skills but knowing how to create one properly can extend the life of your favorite pieces!
Plus, being able to hem clothes yourself opens up greater possibilities when shopping – you’re no longer limited by ‘off-the-rack’ lengths!
Hemming is essential in sewing as it provides functionality (preventing frayed edges) and aesthetics (improving fit). Whether you’re new to sewing or have been at it for years, mastering this technique will surely serve you well!
Exploring the Versatility: Common Types of Hems for Sewing Success
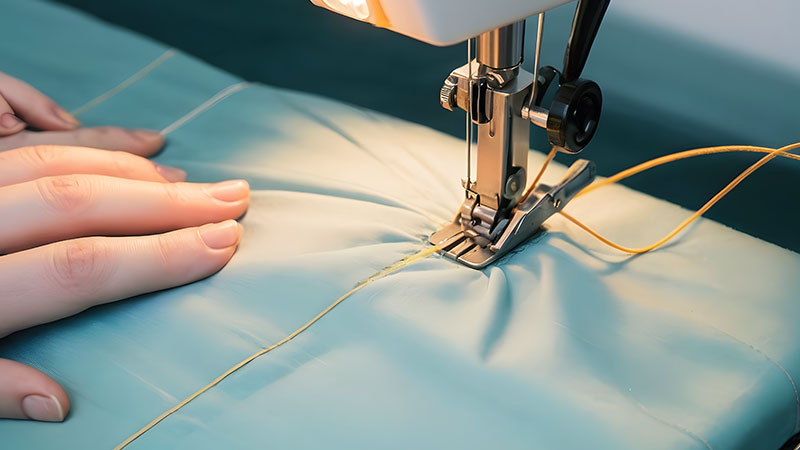
Hems are crucial in giving garments a polished and professional finish while preventing fabric edges from fraying. Several common types of hems are used in sewing, each with unique characteristics and applications.
Rolled Hem
A rolled hem is ideal for lightweight fabrics like silk, chiffon, or organza. In this type of hem, the fabric edge is rolled inward and then stitched down, creating a narrow and neat finish.
Rolled hems are often used on delicate garments where bulkiness needs to be minimized, and a subtle, elegant edge is desired.
Double Fold Hem
The double-fold hem, also known as a double-turned hem, provides a sturdy and clean finish with no raw edges visible.
In this hemming technique, the fabric is folded twice before being stitched down, enclosing the raw edge within the folds.
Double fold hems are commonly used on medium to heavyweight fabrics for garments that require durability and a neat appearance.
Blind Hem
A blind hem is a technique to create nearly invisible hems, particularly on garments like trousers or skirts. Most of the stitching is done on the wrong side of the fabric, with only tiny, discreet stitches catching the front side of the fabric.
This results in a smooth and polished finish on the outside, making the hem practically undetectable from the exterior.
Faced Hem
Faced hems involve attaching a separate facing, or strip of fabric, to the edge of the garment and then folding it inward to create a clean finish.
Faced hems are often used on curved or shaped hems where a traditional folded hem might be challenging to achieve neatly. They also provide additional stability and structure to the hemline.
Bias Bound Hem
Bias-bound hems involve finishing the edge of the fabric with bias tape or binding. Bias tape is cut on the bias grain of the fabric, allowing it to stretch and curve smoothly around curved edges.
This type of hem is suitable for adding a decorative touch to garments or for finishing curved edges such as armholes or necklines.
Essential Tools and Materials for Hemming: A Comprehensive Guide
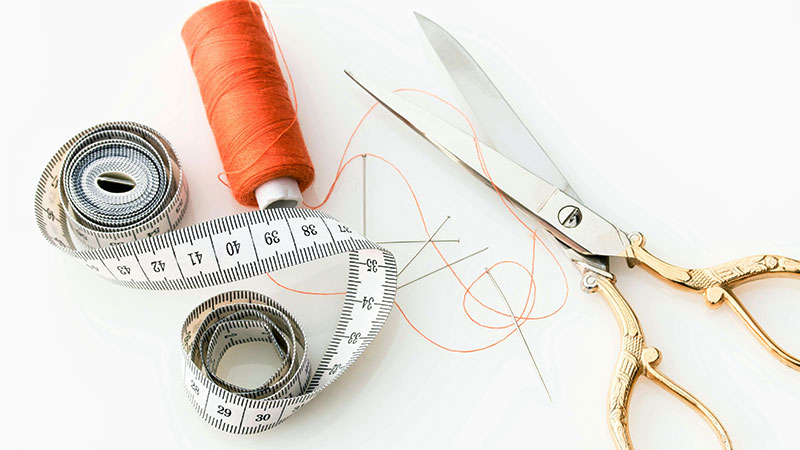
Hemming clothes requires a few essential tools and materials to ensure accuracy, precision, and a professional finish. Here’s a breakdown of the critical items you’ll need:
Measuring Tool
Accurate measurements are crucial for creating even hemlines. A tape measure or sewing gauge allows you to measure the desired length accurately. A sewing gauge is convenient for marking consistent hem widths.
Fabric Marker
A fabric marker marks where you want your new hemline to be. Chalk pencils or water-soluble markers are preferred because they create temporary marks that can be easily removed after sewing, leaving no permanent traces on your garments.
Pins
Pins are essential for securing the fabric in place before sewing. They help ensure the fabric stays aligned and the hem remains even throughout the sewing process. Use them liberally to hold the fabric in position.
Scissors
Sharp scissors specifically designed for cutting fabric are a must-have for hemming. These scissors ensure clean and precise cuts, making it easier to achieve a professional-looking finish. Avoid using dull scissors, as they can result in jagged edges and uneven hems.
Sewing Machine or Needle and Thread
The choice between a sewing machine and hand sewing depends on your preference and the type of hem you’re creating. A sewing machine offers speed and efficiency, ideal for straight hems and larger projects.
Alternatively, needle and thread give you more control and are suitable for delicate fabrics or intricate hand-sewn hems.
Step-By-Step Guide to Hemming: Mastering the Art of Professional-Looking Hems
Hemming clothes is a fundamental sewing skill that can enhance garments’ fit, appearance, and longevity. Whether shortening a pair of pants or giving a dress a polished finish, mastering the art of hemming will serve you well in your sewing endeavors.
Here’s a step-by-step guide to help you hem like a pro:
Measure and Mark
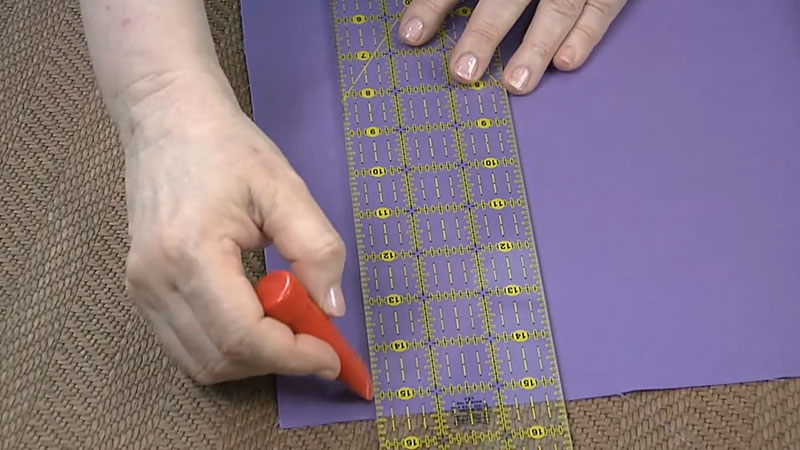
Begin by determining the desired length of the garment. Please put it on and use pins to mark where the new hemline falls. Ensure the garment is hanging straight and the pins are evenly placed.
Prepare the Fabric
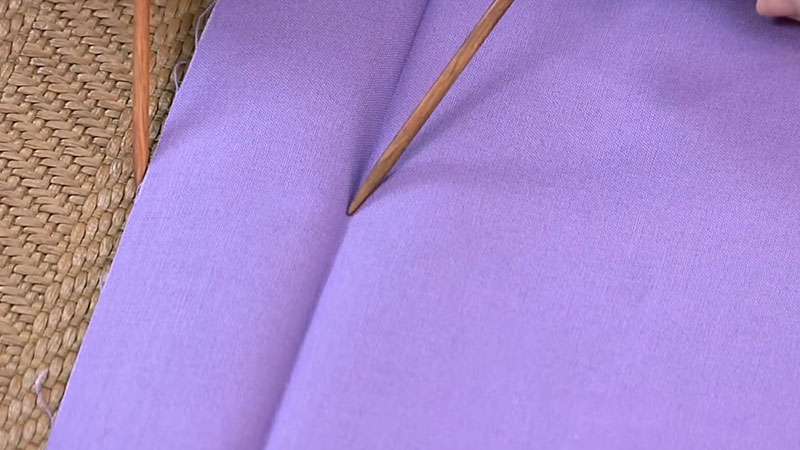
Remove the garment and lay it flat on an ironing board or surface. Fold up the fabric along the pinned hemline, ensuring it’s folded evenly. Use an iron to press along the fold line, creating a crisp crease that will serve as a guide for sewing.
Trim Excess Fabric
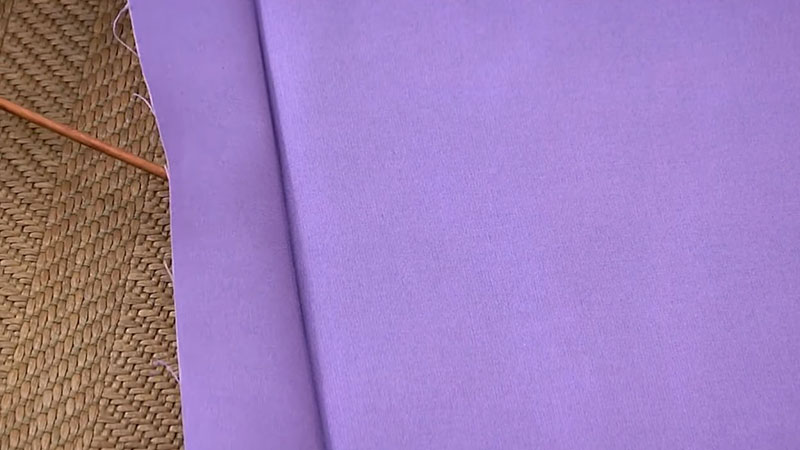
If there’s excess fabric below the folded hemline, trim it down to about one inch. Be careful not to cut too close to the fold line, as you’ll need some allowance for sewing.
Thread the Needle or Machine
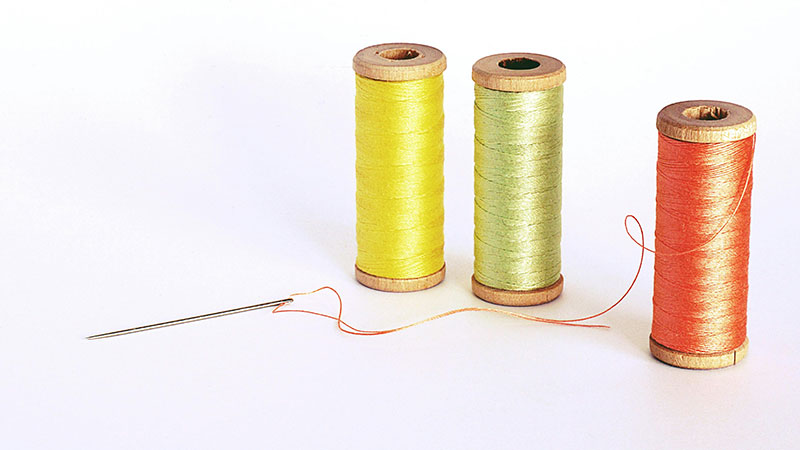
Select a thread that matches the fabric’s color as closely as possible. Thread your needle if you’re sewing by hand, or set up your sewing machine with the appropriate thread and needle for the fabric type.
Secure the Fold
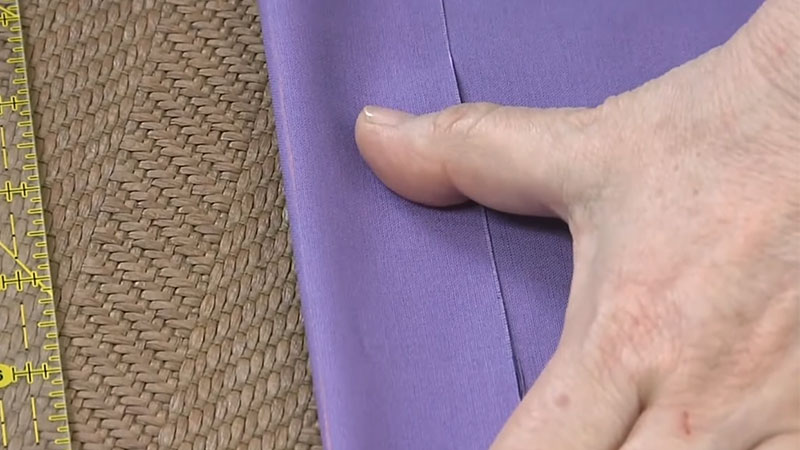
Fold the raw edge of the fabric towards the inside of the garment, encasing it within the fold. Use your fingers to press the fold firmly in place. If desired, pin the fold to ensure it stays put while sewing.
Sew the Hem
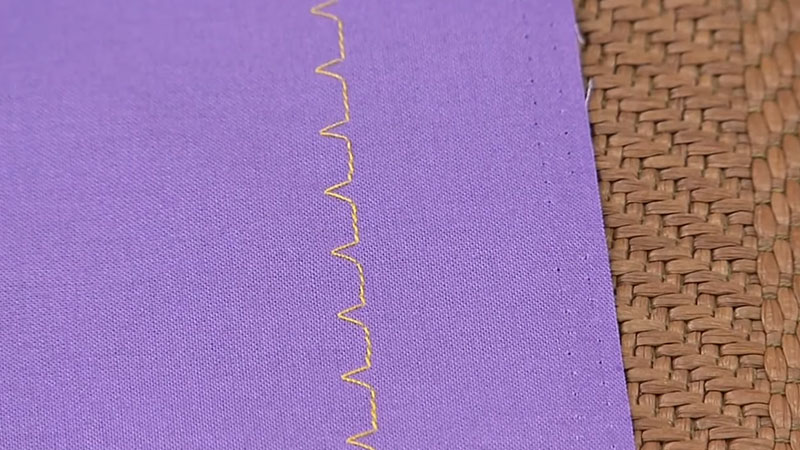
Begin sewing along one edge of the hem, either by hand or using a sewing machine. Use tiny, even stitches for hand sewing to secure the folded edge of the garment. If using a machine, guide the fabric under the presser foot, keeping the stitches close to the folded edge.
Continue sewing all around the hemline until you reach the starting point.
Finish and Press

Once you’ve sewn the entire hem, secure the thread with a knot or backstitch. Trim any excess thread. Finally, give the hem a final press with the iron to set the stitches and ensure a smooth, professional finish.
Mastering Hemming: Tips and Tricks for Professional-Looking Results
A professional hem can elevate the quality and appearance of your sewing projects. Here are some valuable tips and tricks to help you master the art of hemming:
Precise Measurements
Take accurate measurements before hemming to ensure evenness and consistency. Use a ruler or tape measure to determine the desired hem length. Avoid eyeballing, as this can lead to uneven hems that detract from the garment’s appearance.
Ironing
Always iron the fabric along the fold line before sewing. This creates a crisp edge, making sewing easier and ensuring a neat finish. If an iron is not available, use your fingers to press the fold firmly in place.
Hem Tapes or Fusible Webbing
Consider using hem tapes or fusible webbing for delicate or tricky fabrics such as silk or satin. These adhesive tools create clean, seamless hems without the need for stitching. Apply the tape or webbing along the fold line and press with an iron to secure.
Choose the Right Hemming Method
Select the appropriate hemming method based on the garment’s fabric and style. For formal wear, blind hems are ideal as they create nearly invisible seams. Double-folded hems work well for casual items like jeans or linen shirts, providing durability and a clean finish.
Practice
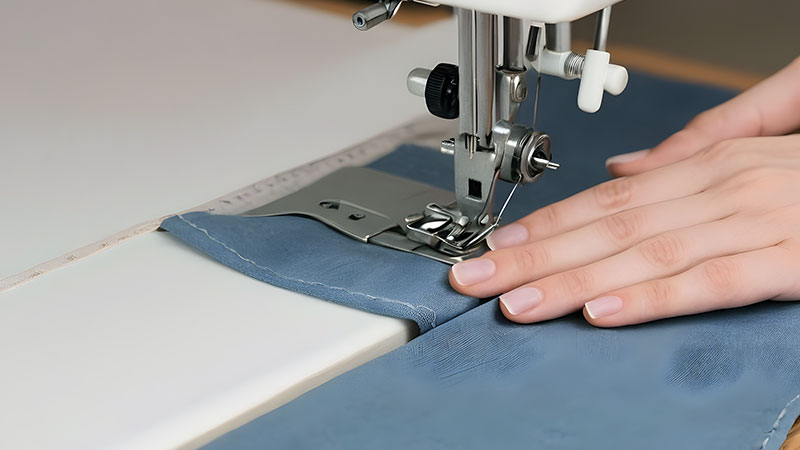
Hemming, like any sewing skill, improves with practice. Don’t be discouraged by initial imperfections—keep practicing and refining your technique. With time and patience, you’ll develop the precision and confidence to create flawless hems.
Finishing Touches
Pay attention to finishing touches such as backstitching or securing the thread ends to prevent unraveling. Trim any excess threads for a polished appearance. Consider using a matching thread color to blend seamlessly with the fabric.
Attention to Detail
Take your time and pay attention to detail throughout the hemming process. Check for any unevenness or puckering as you sew, adjusting as needed to maintain a smooth finish. Attention to detail is critical to achieving professional-looking hems.
Conclusion
I’ve spent the last few paragraphs teaching you what hemming is, how it’s done, and why it’s such a crucial part of sewing. Now that we’re at the end of our journey, I’d like to wrap things up with a few final thoughts.
Hemming clothes isn’t just a skill reserved for professional tailors – anyone can learn how to sew a hem. Whether shortening jeans or adding an elegant finish to homemade curtains, mastering the art of the hem allows you to customize your clothes and home furnishings while extending their lifespan.
Turning over the fabric and sewing it down creates a neat edge that prevents fraying and adds strength. So, whenever someone asks you “what is a hem?”, you’ll have an answer: It’s not just folded fabric it’s an integral part of clothing construction!
While there are different styles of hems for various types of garments and fabrics, they all serve one common purpose: to give your piece a polished look while ensuring its durability.
So next time you find yourself with pants that are too long or drapes that are too short, don’t fret! You’ve got the knowledge of how to hem clothes effectively.
Remember, like any other skill, learning to create the perfect hem takes practice. Don’t get discouraged if your first few attempts don’t happen as planned. Keep trying, keep improving, and you’ll be creating beautiful hems in no time!
And finally – always remember that nothing replaces good old-fashioned craftsmanship, no matter how advanced sewing machines become or how many new techniques we develop.
The quality workmanship in creating each stitch on each hem makes every piece unique – which is something I believe is worth celebrating.
Leave a Reply