Embarking on a sewing journey involves a myriad of tools, each serving a unique purpose in bringing creative visions to life.
Amidst the needles, fabrics, and threads, there’s a discreet yet indispensable ally – carbon paper. Ever wondered what this unassuming sheet contributes to the world of sewing? What is carbon paper used for in sewing?
Carbon paper, traditionally associated with office settings, finds a surprising and valuable application in the realm of stitching.
This unexplored tool plays a crucial role in transferring intricate patterns and designs onto fabrics, streamlining the process of creating precise and professional-looking garments.
As we unravel the mystery behind its role in sewing, we delve into how carbon paper enhances accuracy, efficiency, and creativity in crafting bespoke clothing.
Join us on this exploration of the hidden stitches and patterns that carbon paper unveils in the art of sewing
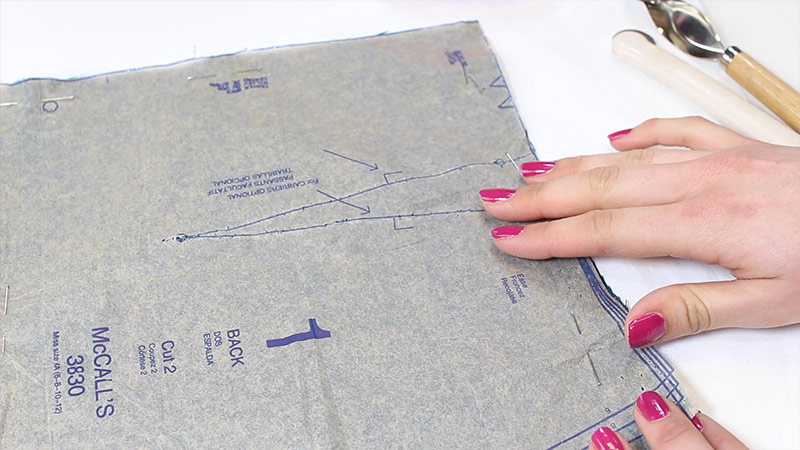
What Is Carbon Paper Used For In Sewing?
Carbon paper is often associated with administrative tasks, and takes on a unique role in the intricate world of sewing. Its application goes beyond traditional office settings, finding a valuable place in the toolkit of sewists worldwide.
Let’s unravel the secrets behind the question: What are the carbon paper for sewing uses?
A Silent Facilitator of Precision
At its core, carbon paper is a thin sheet coated with a layer of dry ink or pigments. In sewing, its primary purpose is to transfer patterns or designs onto fabric surfaces.
This seemingly simple task becomes a game-changer for those who seek precision and accuracy in their creations.
When a sewist wishes to replicate a pattern onto a fabric piece, carbon paper comes into play. Placing the carbon paper between the pattern and the fabric, the user traces the design with a stylus or a pen.
The pressure applied causes the ink on the carbon paper to transfer onto the fabric, creating a clear and accurate outline of the pattern.
This process eliminates the need for freehand drawing directly onto the fabric, ensuring that intricate details are faithfully reproduced.
The Dance of Creativity and Efficiency
Sewing is an art that often demands a delicate balance between creativity and efficiency. Carbon paper contributes significantly to this equilibrium.
By providing a reliable method for transferring patterns, carbon paper for tracing streamlines the preparatory stages of a sewing project, allowing creators to focus more on the artistic aspects of their work.
Imagine the intricate details of an embroidery design or the precision required for quilting patterns. Carbon paper enables the replication of these designs without the risk of distortion or error that may accompany freehand drawing.
This not only saves time but also ensures a higher level of accuracy, especially in projects where precision is paramount.
Tailoring to Individual Needs
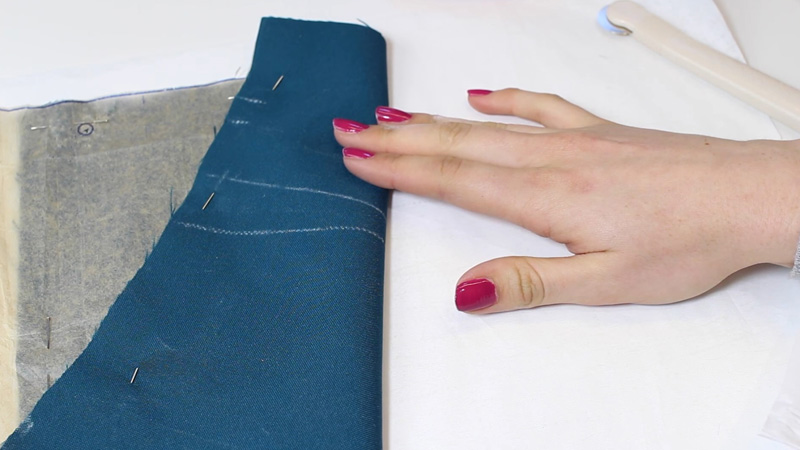
One of the notable advantages of carbon paper for tracing in sewing is its adaptability to various fabrics and projects. Whether you’re working with delicate silk, sturdy denim, or intricate lace, carbon paper proves to be a versatile companion.
Different colors of carbon paper cater to diverse fabric hues, ensuring that the transferred pattern is visible and easy to follow.
Moreover, the thinness of carbon paper allows it to seamlessly conform to the texture of the fabric, capturing even the subtlest details of a design.
For those engaged in custom tailoring or garment alterations, carbon paper facilitates the replication of specific measurements and adjustments.
This adaptability makes it an invaluable tool for sewists catering to a spectrum of client preferences and body types.
From Paper to Fabric: Bridging the Divide
The journey from a conceptualized design on paper to its manifestation on fabric involves intricate steps. Carbon paper acts as a bridge, facilitating a smooth transition between these two realms. It transforms the abstract into the tangible with remarkable accuracy.
This bridging effect is particularly evident in the realm of sewing pattern transfers.
Whether you’re working on a vintage dress pattern from a bygone era or experimenting with a contemporary design of your own, carbon paper ensures that the essence of the pattern is faithfully transferred onto the chosen fabric.
This not only preserves the integrity of the design but also allows for experimentation and customization in the creative process.
Overcoming Challenges with Precision
Sewing often presents challenges that demand precision and attention to detail. Carbon tracing paper emerges as a reliable ally in overcoming these challenges.
For instance, when dealing with intricate lace or sheer fabrics, accurately marking patterns without causing damage can be a daunting task.
Carbon paper offers a solution by providing a non-intrusive method of pattern transfer, allowing for meticulous work without compromising the fabric’s integrity. Moreover, the use of carbon paper minimizes the risk of errors in cutting fabrics.
By having a clear and accurate outline transferred onto the fabric, sewists can confidently cut along the designated lines, reducing the likelihood of mistakes that may arise during the cutting phase.
Sustainability and Cost-Effectiveness
In an era where sustainability is a growing concern, carbon paper aligns with eco-friendly practices in sewing. Its reusability sets it apart from alternatives like tracing paper, which may be discarded after a single use.
Carbon paper, when handled with care, can be employed for multiple projects, making it a cost-effective and environmentally conscious choice for sewists.
The longevity of carbon paper adds to its appeal, making it a staple in the toolkit of those who value efficiency without compromising on sustainability.
This characteristic resonates with a community of sewists increasingly mindful of reducing waste in their creative pursuits.
Carbon Paper for Sewing Uses
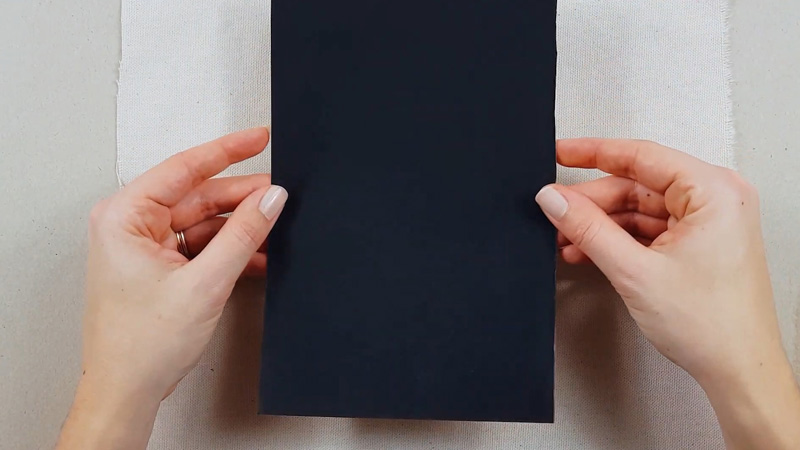
Using carbon paper in sewing is a straightforward yet crucial process that enhances accuracy and efficiency in transferring patterns onto fabric.
Whether you’re a seasoned sewist or a novice, incorporating carbon paper into your toolkit can elevate your projects. Here’s a step-by-step guide on how to use carbon paper in sewing
Prepare Your Work Area
Set up a clean and well-lit work area. Ensure that your fabric is smooth and free of wrinkles. Lay it flat on your work surface, and secure it in place if necessary.
Position the Carbon Paper
Place the carbon paper on top of the fabric with the coated side facing down. Make sure it aligns with the area where you want to transfer the pattern.
Place the Pattern on the Top
Position your pattern or design on the carbon paper, ensuring it sits securely. If the pattern is not already on paper, trace or print it onto a sheet that matches the size of your fabric.
Secure the Layers
To prevent shifting during the tracing process, use small pieces of tape or pattern weights to secure the layers of carbon paper, fabric, and pattern together. This ensures that your pattern stays in place while you trace.
Choose the Right Tracing Tool
Select a suitable tracing tool depending on the fabric and design intricacy. A stylus, a ballpoint pen with no ink, or a tracing wheel are common choices. Be mindful of the pressure you apply to avoid damaging the fabric or creating indentations.
Trace the Design
With a steady hand, carefully trace the lines of your pattern onto the fabric. Apply enough pressure to transfer the ink from the carbon paper onto the fabric but avoid excessive force that may damage delicate fabrics. Ensure you cover all the details of the pattern.
Check Your Progress
Lift a corner of the pattern occasionally to check whether the design is transferring correctly. This helps you catch any missed areas or make adjustments if needed.
Complete the Tracing
Once you have traced the entire pattern, carefully lift off the pattern and carbon paper. Inspect the fabric to ensure that the design has transferred accurately. If any areas need refinement, you can touch them up using a fine-tipped fabric pen.
Secure the Fabric for Cutting
If your project involves cutting the fabric along the traced lines, use fabric weights or pins to secure the fabric layers together. This ensures that the fabric doesn’t shift during the cutting process, maintaining the accuracy of your pattern.
Optional: Multiple Layers and Overlays
Experiment with layering multiple sheets of carbon paper to create intricate designs or overlays. This technique is particularly useful for projects that require detailed embellishments or multiple design elements.
Reuse or Store the Carbon Paper
Carbon paper is often reusable, depending on the care taken during the tracing process. If it’s still in good condition after use, store it for future projects. Proper storage, such as keeping it flat and protected from excessive heat or moisture, extends its lifespan.
Finish Your Sewing Project
With the pattern successfully transferred, proceed with the sewing project as planned. Follow the traced lines for cutting, stitching, or any additional embellishments, ensuring that your final creation reflects the precision achieved through the use of carbon paper.
Tracing Paper Vs Carbon Paper
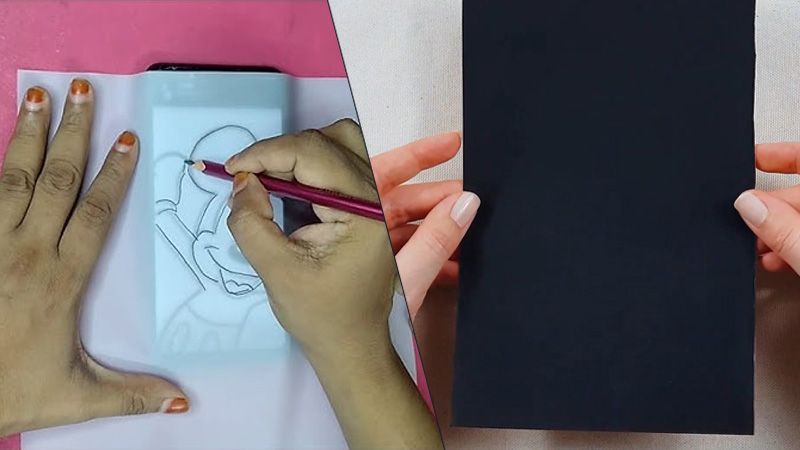
Tracing paper and carbon paper are both tools that play a pivotal role in sewing, aiding in the transfer of patterns onto fabric.
While they serve a similar purpose, each has its distinct characteristics, advantages, and considerations. Let’s explore the differences between tracing paper and carbon paper in the context of sewing.
Tracing Paper
The benefits of using tracing paper are:
Transparency
Tracing paper is transparent, allowing sewists to see the pattern lines clearly as they transfer them onto the fabric. This transparency aids in aligning and adjusting the pattern on the fabric with precision.
Marking Tools
Tracing paper requires a marking tool, such as a pencil or a pen, to transfer the pattern onto the fabric. The pressure applied while tracing determines the intensity of the marks left on the fabric.
Multiple Use
Tracing paper is generally designed for single use, especially if pressure is applied heavily during the tracing process. While some sewists may reuse tracing paper for less intricate designs, it’s not as resilient as carbon paper.
Fabric Compatibility
Tracing paper works well with a variety of fabrics, but its effectiveness can vary depending on the fabric’s texture. It may not adhere as easily to very textured or delicate fabrics.
Adjustability
One advantage of tracing paper is that it allows for adjustments during the tracing process. If you notice an error or want to modify the pattern slightly, you can do so before completing the entire transfer.
Carbon Paper
Here’s how using carbon paper for sewing will be beneficial for you:
Coated with Ink or Pigment
Carbon paper is coated with a layer of dry ink or pigment that transfers onto the fabric when pressure is applied. This coating eliminates the need for an additional marking tool, streamlining the pattern transfer process.
Reusability
Unlike tracing paper, carbon paper is often reusable, especially if used with care. The ink or pigment can endure multiple transfers, making it a more sustainable option for sewers who work on several projects.
Color Variations
Carbon paper comes in various colors, allowing sewists to choose a shade that contrasts well with the fabric. This ensures that the transferred pattern is visible and easy to follow during the sewing process.
Adaptability to Different Fabrics
Carbon paper adapts well to various fabrics, including delicate and textured ones. Its thinness allows it to conform to the fabric’s surface, capturing intricate details without compromising the material.
Precision h4
Carbon paper offers a high level of precision in pattern transfer. The lines transferred onto the fabric are typically sharper and more defined compared to those made with a marking tool on tracing paper.
Choosing Between Tracing Paper and Carbon Paper
Consider the following before choosing a specific type of product for your sewing project:
Project Complexity
For simple designs or projects that require adjustments during the tracing process, tracing paper may be preferable. However, for intricate designs that demand precision and repeated use, carbon paper is a more suitable choice.
Reusability Considerations
If sustainability and cost-effectiveness are priorities, carbon paper’s reusability makes it an attractive option. Tracing paper, being generally single-use, may result in more waste.
Fabric Texture
Consider the texture of the fabric you’re working with. While both tracing paper and carbon paper work well with a variety of fabrics, carbon paper’s adaptability to different textures makes it a versatile choice.
Personal Preference
Sewists may develop a preference based on their working styles and the specific demands of their projects. Some may enjoy the transparency of tracing paper, while others may appreciate the convenience and precision of carbon paper.
FAQs
Can I reuse carbon paper in sewing?
Yes, carbon paper is often reusable. With careful handling and moderate pressure during the tracing process, you can use carbon paper for multiple sewing projects, making it a cost-effective and sustainable option.
Does the color of carbon paper matter in sewing?
Yes, the color of carbon paper matters. Choose a color that contrasts well with your fabric to ensure the transferred pattern is visible and easy to follow during the sewing process. Different colors accommodate various fabric hues.
Can I use carbon paper on textured fabrics in sewing?
Yes, carbon paper is adaptable to different fabrics, including textured ones. Its thin composition allows it to conform to the fabric’s surface, capturing intricate details without compromising the material.
Is tracing paper or carbon paper better for adjustments during sewing?
Tracing paper is more conducive to adjustments during the tracing process. If you need to modify the pattern slightly or make corrections, tracing paper allows for greater flexibility. Carbon paper, on the other hand, offers precision for intricate designs.
What marking tools are suitable for tracing paper in sewing?
Tracing paper requires marking tools such as pencils or pens for pattern transfer. The choice of marking tool depends on personal preference and the fabric type. Ensure the tool leaves a clear and visible mark without damaging the fabric.
Conclusion
As we’ve discussed, the unassuming carbon paper emerges as a silent hero in the world of sewing, elevating the craftsmanship and precision in garment creation.
Its ability to seamlessly transfer intricate patterns onto fabrics empowers sewists to bring their imaginative designs to life with unparalleled accuracy.
As we bid adieu to this often-overlooked tool, let’s not forget the significant role it plays in transforming the mundane into the extraordinary within the realm of needle and thread.
So, the next time you embark on a sewing project, consider the subtle yet impactful presence of carbon paper, facilitating the translation of creativity from paper to fabric, and ultimately, from vision to reality.
As the needle dances and the threads weave, let the subtle mark of carbon paper continue to be a symbol of meticulous craftsmanship in the intricate tapestry of the sewing world.
Leave a Reply