The ultrasonic sewing machine represents a transformative leap in textile manufacturing, revolutionizing how fabrics are joined and sealed.
Unlike traditional methods that rely on needles and thread, this cutting-edge technology utilizes high-frequency vibrations to create heat, seamlessly bonding synthetic fibers together.
Operating on ultrasonic waves, the machine generates rapid vibrations at the molecular level, causing localized heat that melts and fuses fabric layers without stitching.
This innovation finds wide applications in industries such as apparel, automotive, medical textiles, home textiles, technical textiles, and non-woven product manufacturing, offering efficiency, precision, and versatility in fabric processing.
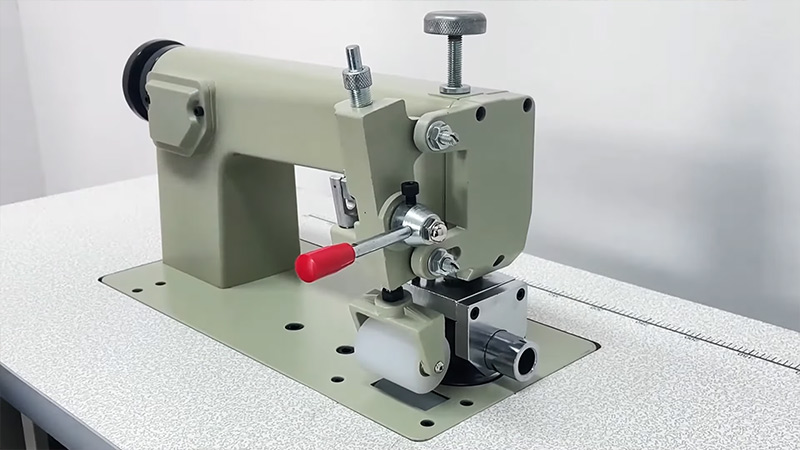
What Is Ultrasonic Sewing Machine?
An ultrasonic sewing machine is a cutting-edge technology in textile manufacturing.
Unlike traditional sewing machines that use needles and thread, ultrasonic sewing machines employ high-frequency vibrations to combine fabrics seamlessly.
These machines utilize ultrasonic waves to create heat, melting and fusing synthetic fibers without stitching.
The process involves placing the fabric layers between the ultrasonic horn and anvil, where the ultrasonic energy generates localized heat.
This heat effectively welds the fabric edges, creating strong and durable bonds. Ultrasonic sewing machines are particularly advantageous for delicate fabrics, as they eliminate the risk of needle damage and reduce fraying.
Additionally, they enhance efficiency by enabling swift and precise cutting and sealing in a single step.
This innovative technology revolutionizes the textile industry, offering speed, precision, and versatility in garment production and other fabric-related applications.
Ultrasonic Sewing Machine Uses
Ultrasonic sewing machines find widespread application in various industries for their versatility and efficiency.
Primarily used in textile manufacturing, these machines excel in bonding and sealing synthetic fabrics without the need for traditional stitching.
The applications of ultrasonic sewing machines include:
Apparel Industry
In fashion and apparel manufacturing, ultrasonic sewing machines offer a cutting-edge alternative to traditional stitching methods.
They excel in seamlessly joining fabric layers, creating a sleek and modern aesthetic without the need for visible stitches.
This technology is particularly advantageous for delicate and lightweight fabrics like chiffon, silk, and other synthetics, where traditional sewing might cause damage or distortion.
The precision of ultrasonic welding ensures that garments maintain their structural integrity while achieving a clean and professional finish, meeting the high standards of the fashion industry.
Automotive Upholstery
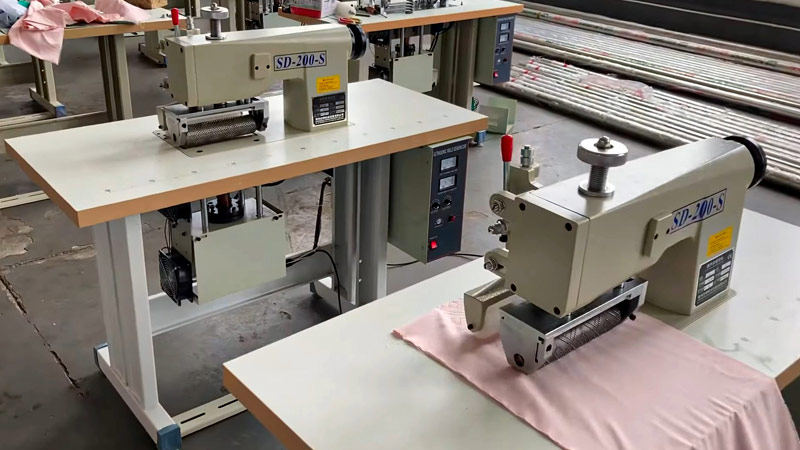
Ultrasonic sewing machines play a crucial role in the automotive sector, specifically in assembling and binding materials for vehicle interiors.
These machines provide a seamless and durable solution, from seat covers and door panels to headliners.
The technology ensures that the fabrics used in automotive upholstery are securely bonded, enhancing the interior components’ aesthetic appeal and longevity.
The efficiency and precision of ultrasonic welding contribute to producing high-quality automotive textiles, meeting the industry’s stringent requirements.
Medical Textiles
In medical textiles, the unparalleled precision and cleanliness of ultrasonic welding make it an indispensable technology.
It is extensively used to manufacture surgical gowns, masks, and various disposable medical supplies.
The stitch-free, sealed seams created by ultrasonic sewing machines contribute to the sterility and durability of these critical medical products, meeting the stringent standards of hygiene and safety required in healthcare settings.
Home Textiles
Ultrasonic sewing machines offer a transformative approach for bedding, curtains, and other home textile products.
The seamless, stitch-free finish enhances the visual appeal of these products and contributes to their functionality.
Home textiles benefit from the durability and strength of ultrasonically welded seams, ensuring that products withstand regular use and washing while maintaining their original quality and appearance.
Technical Textiles
Industries involved in technical textiles, such as geotextiles, filtration, and industrial fabrics, leverage ultrasonic sewing to create robust and reliable seams in specialized materials.
Whether it’s reinforcing materials for construction, filtration systems, or industrial components, the precision of ultrasonic welding ensures that these textiles meet the rigorous demands of their respective applications.
Non-woven Products
Ultrasonic technology is preferred in producing non-woven products like disposable diapers, hygiene items, and filters.
The strength and integrity of the bonds created by ultrasonic sewing machines are crucial for ensuring the reliability and performance of these products.
The stitch-free nature of the seams adds to the comfort and functionality of disposable items while maintaining the structural integrity of non-woven materials.
This makes ultrasonic technology a key player in producing various everyday essentials.
How Does an Ultrasonic Sewing Machine Work?
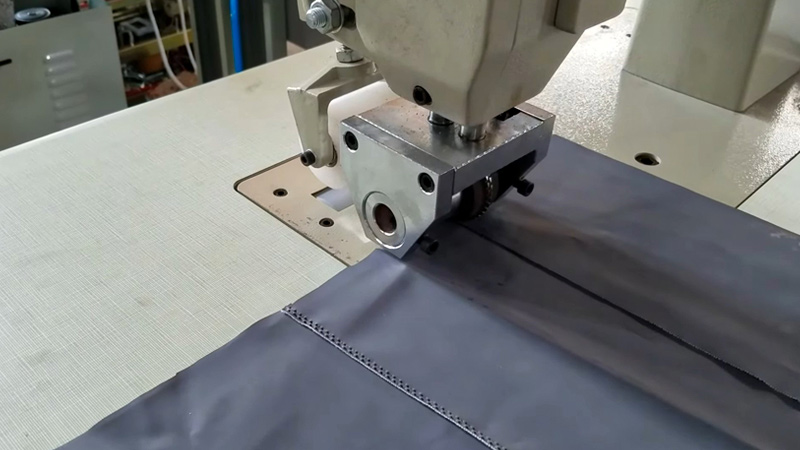
An ultrasonic sewing machine converts electrical energy into high-frequency mechanical vibrations, specifically ultrasonic waves, to join fabrics together.
The process involves several key components and steps:
Generator and Transducer
The ultrasonic generator is at the heart of an ultrasonic sewing machine, which serves as the power source.
This generator produces electrical energy, typically from 20 to 40 kHz. This electrical energy is then channeled to the transducer, a critical component that converts the electrical energy into high-frequency mechanical vibrations.
The transducer functions akin to a speaker, transforming the electrical input into oscillations that will be used to create ultrasonic waves.
Converter and Horn
The transducer is connected to a converter, an element that further amplifies the mechanical vibrations generated. The amplified vibrations are then directed towards the ultrasonic horn, a sonotrode.
The horn is crucial in concentrating and transmitting the vibrational energy to the fabric.
It is often designed to match the processed materials’ specific requirements, ensuring optimal energy transmission efficiency.
Fabric Placement
In fabric welding, the joint layers are strategically placed between the ultrasonic horn and an opposing tool, commonly an anvil or a countertop.
The fabric is carefully positioned, ensuring proper alignment and contact with the ultrasonic horn. This configuration forms a sandwich-like structure, allowing the ultrasonic waves to pass through the material efficiently.
Vibration and Heat Generation
As the ultrasonic waves encounter the fabric, they induce rapid vibrations at the molecular level. These vibrations create friction within the fabric, generating localized heat.
The heat results from the intense molecular movement, causing the synthetic fibers in the fabric to reach their melting point. This controlled and localized heating process is fundamental to the success of ultrasonic welding.
Bonding and Sealing
Applying heat from the ultrasonic waves causes the synthetic fibers in the fabric to melt. As a result, the adjacent fabric layers fuse, creating a robust and durable bond.
This bonding process is particularly effective for synthetic fabrics, where the melted fibers solidify upon cooling.
The outcome is a seamless, stitch-free seam or bond with strength and aesthetic appeal.
Cutting
For added efficiency, some ultrasonic sewing machines are equipped with cutting blades. These blades are positioned near the ultrasonic horn and can trim excess fabric during welding.
This simultaneous cutting and sealing capability streamlines production processes, saving time and enhancing precision.
It is especially beneficial for applications where precise cutting is integral to the final product, offering a seamless integration of fabric joining and trimming in a single step.
Ultrasonic Sewing Machine Prices
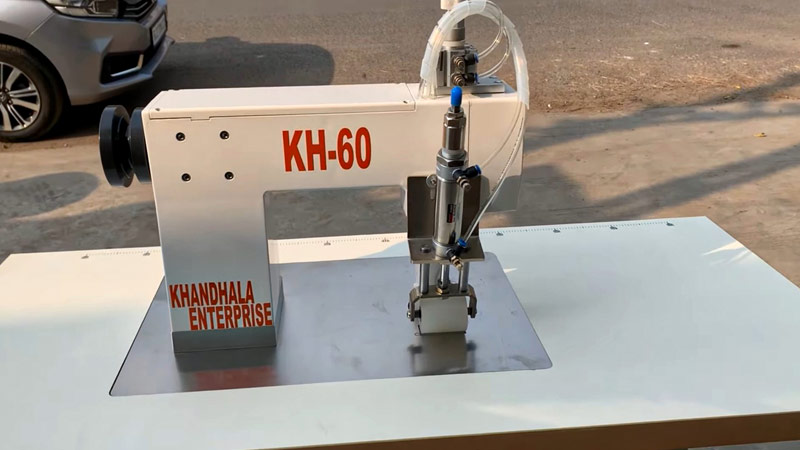
Ultrasonic sewing machines have become pivotal in modern textile industries, offering efficient and precise fabric joining without traditional stitching.
As businesses explore integrating this advanced technology into their production processes, understanding the range of ultrasonic sewing machine prices becomes essential.
The cost of these machines can vary based on factors such as brand, features, and production capacity.
Below is a concise table outlining approximate prices for ultrasonic sewing machines:
Table: Ultrasonic Sewing Machine Prices (Approximate Ranges)
Brand/Model | Features | Production Capacity | Frequency Range | Additional Information | Price Range (USD) |
SoniXtra 2000 | Entry-level model for small-scale production | Low to Medium | 20 – 30 kHz | Compact design, ideal for startup businesses | $5,000 – $8,000 |
UltraBond Pro 5000 | Mid-range with enhanced features | Medium to High | 25 – 35 kHz | Digital controls, adjustable power settings | $10,000 – $15,000 |
SonicSeal Max 8000 | High-capacity, industrial-grade machine | High | 30 – 40 kHz | Programmable stitching patterns suitable for technical fabrics | $20,000 – $30,000 |
Precision Stitch 3000 | Precision welding for delicate fabrics | Low to Medium | 20 – 30 kHz | Specialized for lightweight and delicate materials | $8,000 – $12,000 |
TechFusion Master X | Advanced features for technical textiles | High | 25 – 35 kHz | Programmable stitching patterns, suitable for technical fabrics | $15,000 – $25,000 |
FAQs
Is an Ultrasonic Sewing Machine suitable for all fabrics?
While particularly effective with synthetics, ultrasonic sewing machines are versatile and handle various materials, excelling in delicate and lightweight fabrics.
Are Ultrasonic Sewing Machines cost-effective in the long run?
Despite the initial investment, ultrasonic sewing machines often prove cost-effective due to increased efficiency, reduced labor costs, and minimal material wastage over time.
To Recap
The ultrasonic sewing machine emerges as a transformative force in textile production, transcending conventional sewing methods.
Its ability to fuse fabrics seamlessly through high-frequency vibrations brings efficiency, precision, and versatility to various industries.
The stitch-free, heat-induced bonding ensures durability and enhances the aesthetic appeal of end products.
From delicate apparel to industrial applications, the ultrasonic sewing machine proves indispensable.
As technology advances, this innovative tool redefines the landscape of fabric joining, offering a clean, rapid, and reliable alternative.
Its impact resonates across sectors, reaffirming its status as a cornerstone in modern textile manufacturing, poised for further advancements.
Leave a Reply