you’re in the middle of a fantastic sewing project, and suddenly, your thread breaks! It’s a universal frustration among sewing enthusiasts, whether you’re a seasoned pro or just starting.
Thread breakage can bring your creative flow to a screeching halt, leaving you feeling puzzled and discouraged. But don’t worry!
This comprehensive guide is here to help you unravel the mysteries of thread breakage, providing insightful solutions and preventive tips to keep your sewing machine humming happily.
We’ll examine the usual suspects behind thread breakage and offer straightforward solutions to get you back on track
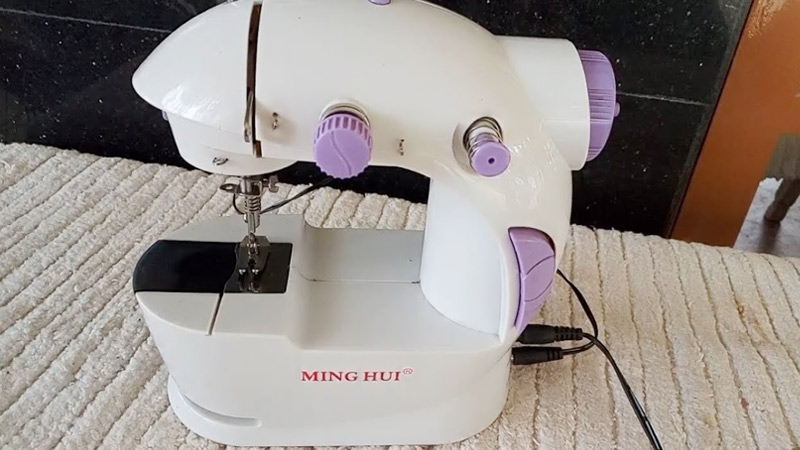
1. Top Thread Threaded Incorrectly
It’s easier than you think to miss a step when threading your machine, even if you’ve done it a thousand times. A missed thread guide or tension disk can lead to snags and breaks.
Solution: Always refer to your machine’s manual for threading instructions specific to your model. Rethread your top thread carefully, ensuring it passes through each guide and tension disk correctly.
2. Incorrect Top Thread Tension
Thread tension is like Goldilocks—it needs to be just right. When the tension is too tight, it puts excessive stress on the thread, causing it to snap.
Solution: Try loosening the top thread tension slightly. Test the tension on a scrap piece of fabric that matches your project fabric to ensure a balanced stitch.
3. Bobbin Tension Needs Adjustment
Most sewing machine manufacturers recommend leaving the bobbin tension as is. However, sometimes it needs a slight tweak to balance the tension with your top thread.
Solution: If adjusting the top thread tension doesn’t fix the problem, carefully loosen the bobbin tension. Use a scrap of fabric to test the tension and ensure your stitches are balanced.
4. Needle Inserted Incorrectly
It might seem simple, but inserting the needle backward or not pushing it up as far as it can go is a common mistake. This can cause it to hit the throat plate or bobbin case, breaking the needle and/or thread.
Solution: Check the needle shank. It has a flat side that should face the back of the machine. Make sure the needle is inserted all the way up and is securely tightened.
5. Needle Is Damaged
Even a slight bend, dullness, or burr on your needle can wreak havoc on your thread.
Solution: Regularly inspect your needle for any signs of damage, like a dull tip or a bent shaft. Replace damaged needles immediately. Investing in good-quality needles and changing them frequently will save you a lot of headaches (and broken threads!)
6. Bobbin Is Wound Unevenly
An unevenly wound bobbin can cause the thread to catch and tangle, leading to breaks.
Solution: Slow and steady wins the race when winding your bobbin. This ensures the thread is distributed evenly. If you’re still having problems, consider replacing the washer on the bobbin winder.
7. Lint Buildup in the Machine
Tiny bits of thread and fabric accumulate over time, creating lint buildup that can interfere with your machine’s performance.
Solution: Make cleaning your machine a regular habit! Pay special attention to the bobbin case and under the needle plate, where lint loves to hide.
8. Mismatched Thread Types or Weights
Using different thread types or weights for your top thread and bobbin thread can cause tension problems and breakage.
Solution: Choose threads that are compatible with each other and your fabric. Use the same type and weight of thread in both the needle and bobbin. Winding your own bobbins ensures a perfect match.
9. Spool Not Correctly Placed or Wrong Type Used
The way you position your spool and the type of spool you use can affect the thread tension. Sewing machines can have vertical or horizontal spool pins, and the type of thread winding on the spool matters (cross-wound or parallel wound).
Solution: Check your sewing machine manual to determine the correct spool placement for your model. Ensure you are using the correct type of thread winding for your spool pin. For example, use parallel wound thread with old-style vertical pins.
10. Bobbin Not Inserted Correctly
Even a slightly misplaced bobbin can lead to thread jams and breaks.
Solution: Double-check that your bobbin is properly inserted in the bobbin case and that the thread is threaded correctly. Refer to your sewing machine manual for guidance.
11. Thread Catching on the Spool
Sometimes, one end of the spool has a rough spot to hold the thread end. If the spool is installed incorrectly, this rough edge can snag the thread and cause it to break.
Solution: Ensure the thread is feeding off the spool smoothly and in the correct direction. Refer to your machine manual for the proper way to install your spool.
12. Thread Wrapping Around Spool Pin
If the thread wraps around the spool pin under the spool cap, it can cause tension and breakage.
Solution: Use a spool cap that fits your spool snugly to prevent the thread from slipping under it. If you notice thread wrapped around the pin, unwrap it, rethread the machine, and continue sewing.
13. Thread Getting Caught on a Thread Guide
The thread guides on your machine help direct the thread, but if the thread isn’t threaded through them properly, it can snag or wrap around them, leading to breakage.
Solution: Carefully follow your machine’s threading diagrams or the instructions in your manual. Make sure the thread is properly seated in each guide.
14. Thread Not Suitable for the Fabric or Machine
Using a thread that’s too fine for your fabric or a thread type that your machine isn’t designed for can lead to problems. For example, using embroidery thread on a regular sewing machine can cause breakage.
Solution: Select thread that’s appropriate for both your fabric and your sewing machine. Consider the fabric weight and the project requirements.
15. Spool Cap is the Wrong Size
A spool cap that doesn’t fit properly can cause the thread to tangle or get caught.
Solution: Make sure you are using a spool cap that’s the correct size for your thread spool and that it is securely in place.
16. Thread is Old or Damaged
Like many things, thread can degrade over time. Old thread can become weak and brittle, making it prone to breaking.
Solution: Store thread in a cool, dark place to extend its lifespan. Avoid using old or damaged thread, even if it’s a vintage find!
17. Thread Quality Is Poor
You might be tempted by bargain-basement thread prices, but low-quality thread can lead to a lot of frustration. It’s more likely to break and can also cause tension issues.
Solution: Invest in good-quality thread from a reputable brand. It will save you time and frustration in the long run!
18. Using a Bobbin Not Made for Your Machine
Bobbins come in slightly different sizes, and using the wrong one can cause it to bounce around in the bobbin case, leading to thread breaks.
Solution: Always use bobbins specifically designed for your sewing machine model.
19. Bobbin is Damaged
Plastic bobbins can warp from the heat generated during sewing, and even metal bobbins can get damaged.
Solution: Store your bobbins in a cool, dry place. If your bobbin thread keeps breaking, try a new bobbin.
20. Needle and Thread Don’t Match the Project
Different sewing projects require different needles and thread types.
Solution: Always select a needle and thread that are appropriate for the fabric you are working with and the type of sewing you are doing. For example, heavy fabrics will require a sturdier needle and thicker thread.
21. Needle Plate Is Damaged
A damaged needle plate can create burrs or rough spots that can snag and cut your thread.
Solution: Examine your needle plate for any damage. If you find any, it’s time to replace it with a new one.
22. Needle Hitting the Needle Plate
A loose, bent, or incorrectly inserted needle can strike the needle plate, causing damage and thread breaks.
Solution: Carefully remove your needle and inspect it for any bends. Ensure it is inserted correctly and securely tightened. If the needle plate is damaged, replace it.
23. Needle Coming into Contact with the Presser Foot
If your presser foot is positioned too high or not correctly aligned, the needle can hit it, leading to thread breaks.
Solution: Adjust the height of your presser foot so that it rests lightly on the fabric surface when lowered. Check both the needle and presser foot for any damage and replace them as needed.
Leave a Reply